Enhancing Fiberglass Components for a Leading Window and Door Manufacturer
Summary
Acme Mills partnered with a leading North American window and door manufacturer to supply high-performance polyester veils designed to enhance the durability and aesthetic quality of their pultruded fiberglass components. The project required the production of veil material, used primarily in manufacturing door and window frames. These materials, critical for their UV resistance, surface finish, and chemical protection properties, were delivered on schedule, meeting the exacting standards of the client.
Project Specifications
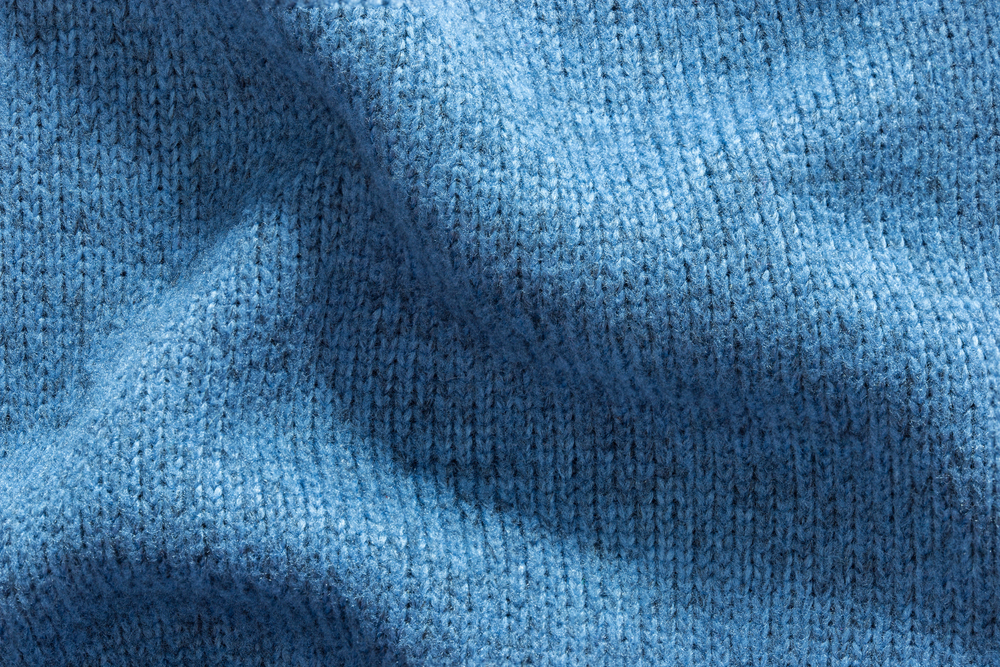
Applications & Capacity
Uses and Applications
The veil material supplied by Acme Mills is integral to the pultrusion process, offering the following advantages:
- Enhanced Surface Finish: Provides a smooth outer layer to improve the visual quality of pultruded components.
- UV Resistance: Acts as a barrier against ultraviolet degradation, essential for long-term outdoor exposure.
- Surface Protection: Minimizes defects such as fiber visibility and resin-rich areas, ensuring uniformity.
- Chemical Resistance: Adds protection against corrosive substances, enhancing longevity.
Capacity and Scalability
Acme Mills demonstrated the capacity to scale production efficiently, delivering large quantities of veil material within tight deadlines. The company’s advanced manufacturing capabilities enabled it to handle both small-scale custom orders and high-volume production runs while maintaining quality and precision.
Manufacturing Details
1. Material Selection and Preparation
The polyester veils were produced using high-quality polyester fibers. Two variants were tailored to meet the client’s specific requirements:
0.234 oz/yd² veil for lightweight applications.
0.50 oz/yd² veil for applications requiring additional strength and durability.
2. Production Process
Slitting and Re-Rolling: Rolls of polyester material were slit to specified widths and re-rolled for ease of use in the pultrusion process.
Flat Bonding: The material was precision-bonded to ensure uniform density and strength.
Customization: Each roll was labeled and prepared per the client’s exact specifications for direct integration into their production lines.
3. Quality Control
Acme Mills adheres to rigorous quality control measures to ensure consistency and performance:
Material Testing: Polyester fibers underwent tensile strength and weight validation before production.
Visual Inspection: Each roll was inspected for defects, including uneven bonding or visible impurities.
Dimensional Checks: Rolls were verified for uniform width and roll length as per purchase order specifications.
Lot Tracking: Materials were batch-numbered for traceability, ensuring accountability and streamlined resolution of any client inquiries.
Acme Mills successfully executed this project by aligning its manufacturing capabilities with the client’s stringent requirements. The partnership highlights Acme Mills’ expertise in producing specialized materials for the pultrusion industry, contributing to the enhanced durability, performance, and aesthetic quality of fiberglass components. This case study serves as a testament to the company’s commitment to quality, reliability, and innovation in textile manufacturing for industrial applications.