Designing a Fire Retardant Duct Wrap for HVAC Systems in Response to Regulatory Changes
Needs Assessment & Solutions Summary
A leading HVAC manufacturer in the commercial, industrial, and residential markets faced a critical challenge when regulatory changes rendered their existing foam fire retardant material noncompliant. This regulatory shift necessitated a solution that met UL 181 standards for fire retardancy while maintaining system performance.
Great Lakes Filters collaborated closely with the client to design a custom fire-retardant material capable of wrapping existing ductwork. This new solution improved safety and reduced operational noise, ensuring compliance and enhancing the product’s marketability. By leveraging innovative material treatments and advanced manufacturing techniques, Great Lakes Filters delivered a solution that balanced performance, compliance, and scalability.
The project outcome ensured the client maintained production continuity, enhanced system performance, and adhered to updated regulations without disrupting their supply chain.
Project Specifications
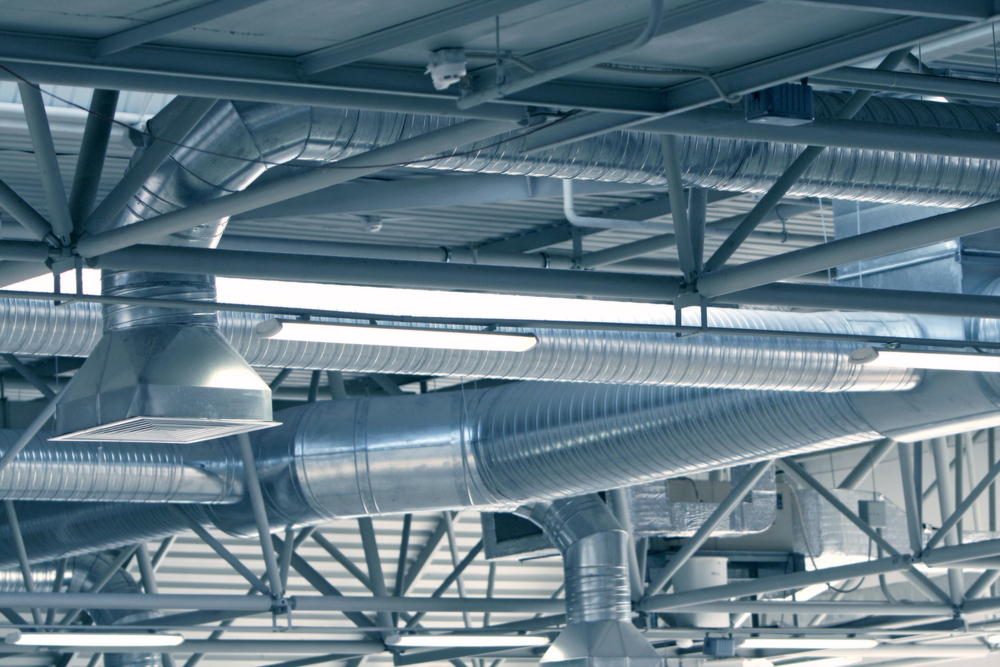
To address these challenges, Great Lakes Filters developed a bromine-free, fire-retardant material with optimized strength and acoustic properties. Key components of the solution included:
- Applications: Fire-retardant duct wrap for HVAC systems used in commercial, industrial, and residential settings.
- Capacity: Scalable production to support the client’s national supply chain needs, ensuring seamless integration with existing operations.
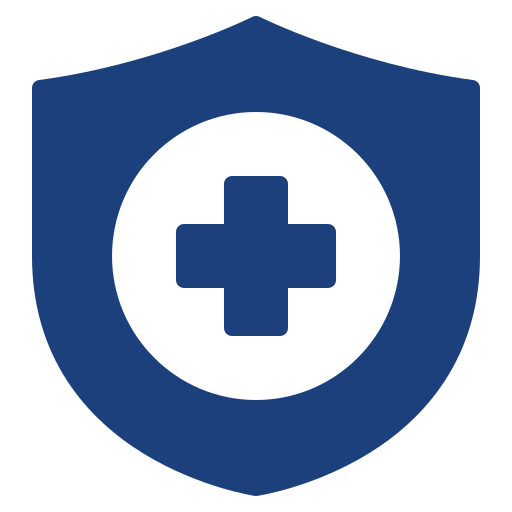
Healthcare
Fire-safe and noise-reducing duct wraps for hospitals and clinics.
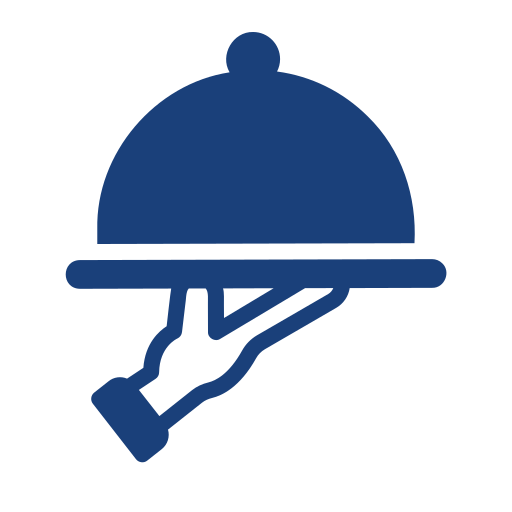
Hospitality
Enhanced HVAC safety and acoustic performance for hotels and restaurants.
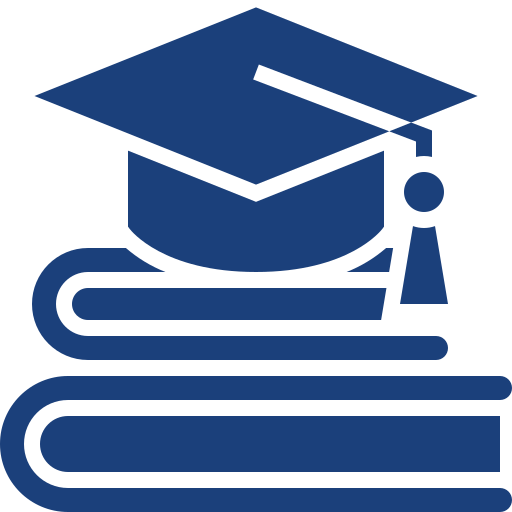
Education
Compliance-driven HVAC solutions for schools and universities.
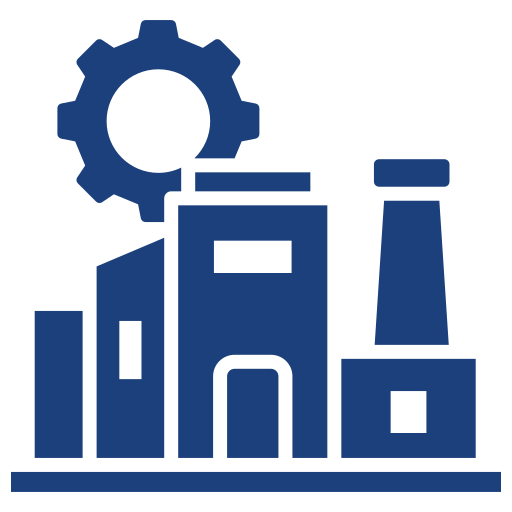
Manufacturing
Industrial facilities requiring
fire-retardant HVAC systems.
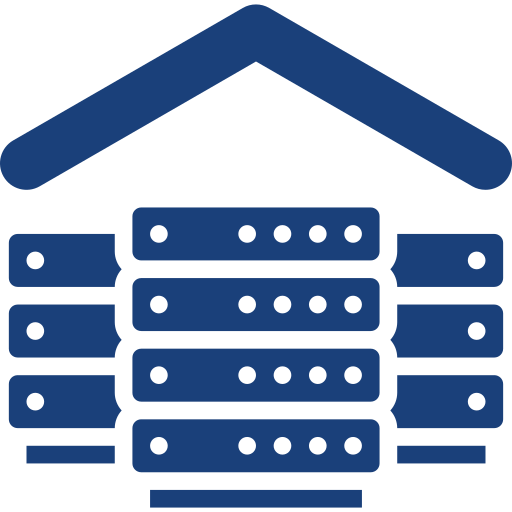
Data Centers
Ensuring safety and system reliability
in critical cooling environments.
Manufacturing Details
Material Sourcing:
Selected high-durability base materials compatible with fire-retardant treatments.
Fire Retardant Application:
Applied a bromine-free fire retardant treatment tailored for compliance with UL 181.
Fabrication:
Produced the material in roll form for easy integration into existing manufacturing lines.
Quality Control Measures:
Conducted UL 181 fire resistance and tensile strength tests.
Verified material consistency and uniformity across production batches.
Maintained comprehensive documentation, including Material Safety Data Sheets (MSDS).
Quality Control Highlights
Great Lakes Filters implemented rigorous quality control protocols to ensure the material met the client’s requirements:
Value Delivered
This project demonstrates Great Lakes Filters’ expertise in developing innovative, customized solutions for complex regulatory and operational challenges. By designing a new fire-retardant material tailored to the client’s requirements, Great Lakes Filters ensured compliance, improved system performance, and supported scalable production needs.