Optimizing Central Coolant Systems for a North American Automotive Powertrain Supplier
Needs Assessment & Solutions Summary
Great Lakes Filters partnered with a leading automotive supplier of powertrain components in North America to address severe maintenance challenges with their central coolant system. The client operated a 50,000-gallon system that supplied coolant to multiple machining centers critical to their production. Trap oil contamination and hydraulic leaks had disrupted operations, leading to tooling running hot, excessive machining chatter, and unacceptable part quality. These issues not only increased tooling and maintenance costs but also caused frequent downtime, creating a significant bottleneck in production schedules.
The client faced additional constraints, including the inability to perform full coolant system dumps due to the prohibitive cost of waste treatment and downtime. They needed a solution that would allow for efficient filtration and cleaning without halting operations or degrading the lubricity of their water-soluble coolant.
Great Lakes Filters developed a progressive solution involving multiple composite filter roll media tailored to the specific stages of filtration required. This approach allowed the client to gradually clean and balance their system while maintaining optimal performance, leading to improved part quality, extended coolant life, and reduced waste treatment costs. The solution not only restored the efficiency of their production processes but also provided a safer, cleaner working environment for their team.
Project Specifications
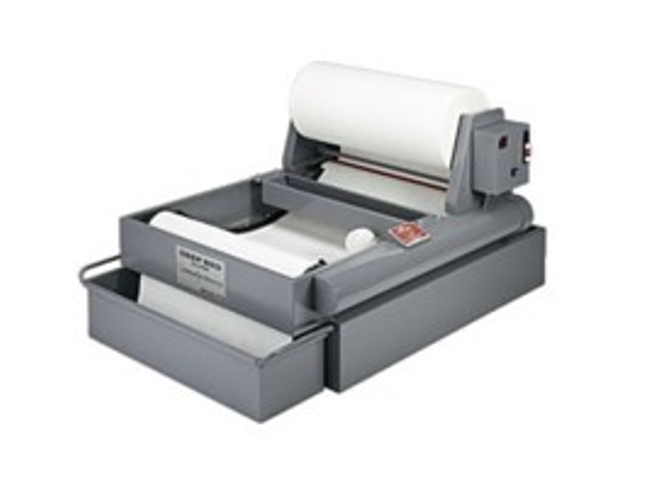
To address these challenges, Great Lakes Filters engineered a set of three filter roll media designed for intermittent use:
- The solution enabled periodic cleaning of the coolant system without requiring complete system dumps.
- Supported consistent coolant filtration for extended periods, reducing the frequency of media replacement.
- Ensured machining centers operated within specified tolerances, improving overall productivity.
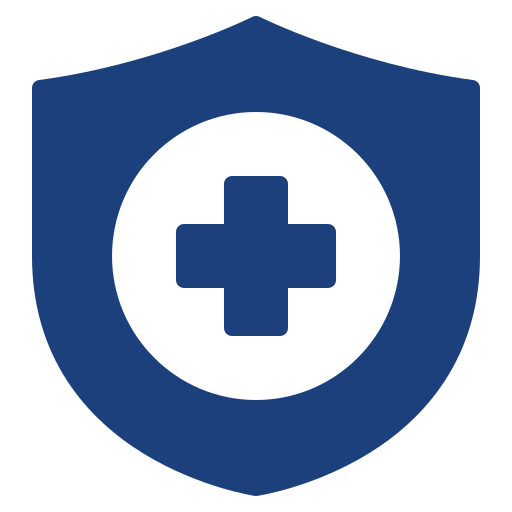
Aerospace Manufacturing
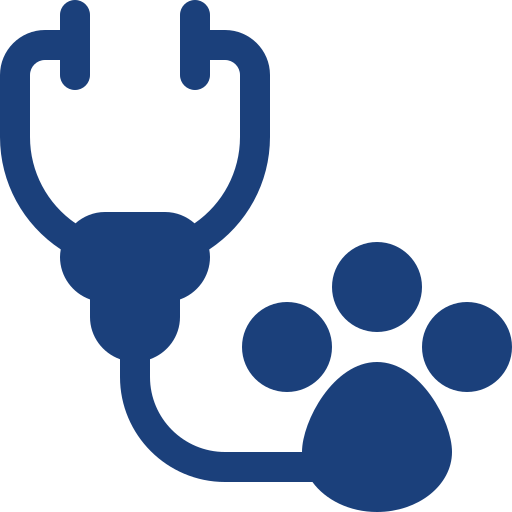
Heavy Equipment and Machinery Production
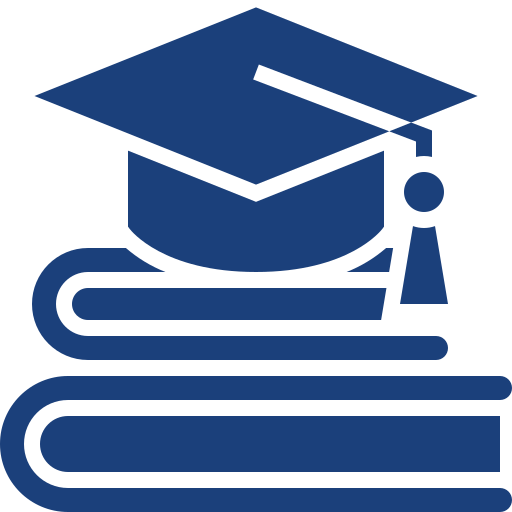
Industrial Pump and Compressor Manufacturing
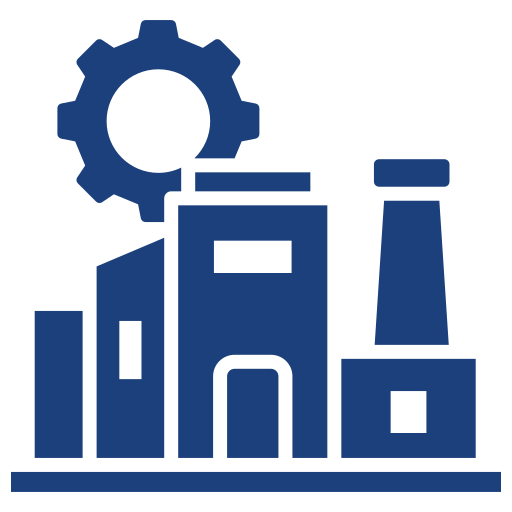
Metalworking and Fabrication
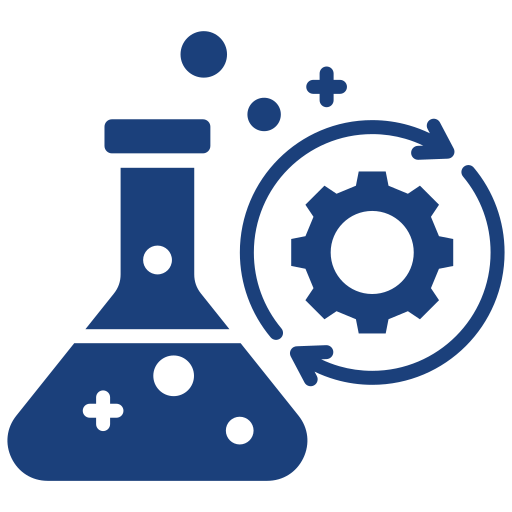
Energy and Power Generation Equipment
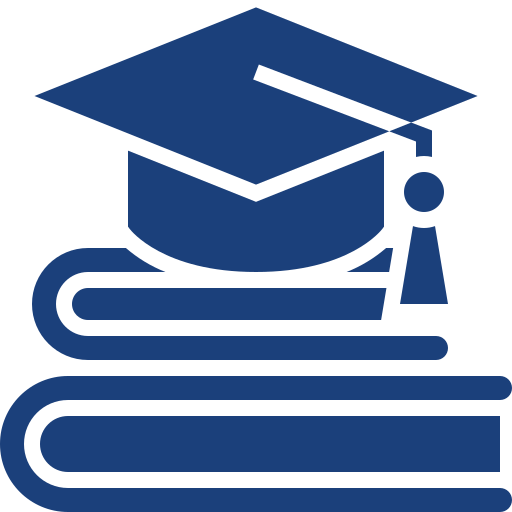
Marine and Shipbuilding Industries
Manufacturing Process
Composite Construction
The filter rolls were crafted from ISO-certified oleophilic and oleophobic materials.
Customization
The composition and layering of materials were optimized to ensure high performance without premature media blinding.
Batch Testing
Each roll underwent stringent quality control to verify its filtration capacity and durability.
Quality Control Measures
Great Lakes Filters adhered to stringent quality assurance protocols to meet the client’s rigorous pharmaceutical standards:
Value Delivered
This project underscores Great Lakes Filters’ capability to deliver innovative filtration solutions that address complex industrial challenges. By tailoring the composition and application of filter roll media, the client achieved operational efficiency, cost reductions, and improved product quality.