Restoring Dust Collection Efficiency for a Southeastern Michigan Electrical Energy Producer
Needs Assessment & Solutions Summary
Great Lakes Filters collaborated with a leading electrical energy producer in Southeastern Michigan to resolve compliance issues with EPA PM10 emission standards. The client faced severe challenges due to aging and inefficient dust collection equipment, including damaged housing and compromised filter bags in a 50-year-old system. These deficiencies not only hindered compliance but also caused significant operational disruptions, necessitating a sectional shutdown of the facility.
The client required a high-temperature filtration solution to withstand a corrosive environment while maintaining the system’s original design functionality. Leveraging decades of experience and an extensive library of dust collection system designs, Great Lakes Filters reverse-engineered and optimized the replacement dust bags to enhance durability and performance. In addition, system-wide inspections and updates were implemented to restore the system’s self-cleaning functionality and operational efficiency.
The comprehensive solution provided by Great Lakes Filters ensured compliance with EPA standards, reduced downtime, and extended the system’s lifespan, allowing the plant to operate at full capacity.
Project Specifications
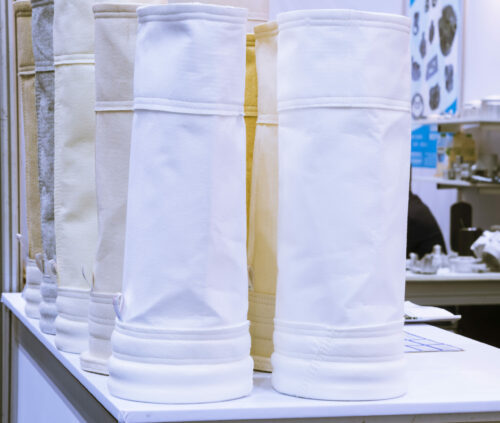
To address these challenges, Great Lakes Filters developed a tailored approach combining reverse engineering and system optimization:
- Applications: Dust collection for particulate emissions in power generation.
- Capacity: Improved system efficiency allowed uninterrupted operation of the affected power generation section, restoring compliance and operational output.
Other industries that could benefit from this solution include:
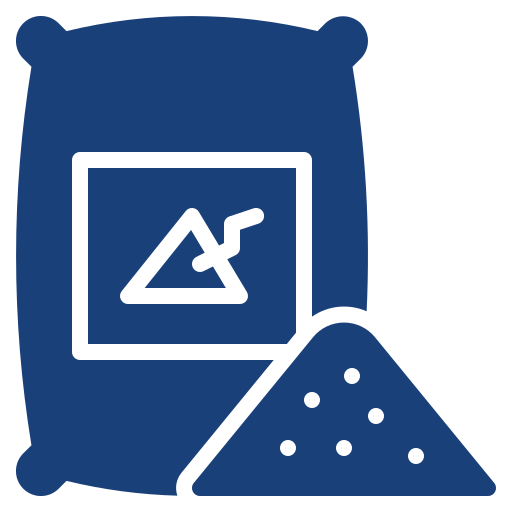
Cement Manufacturing
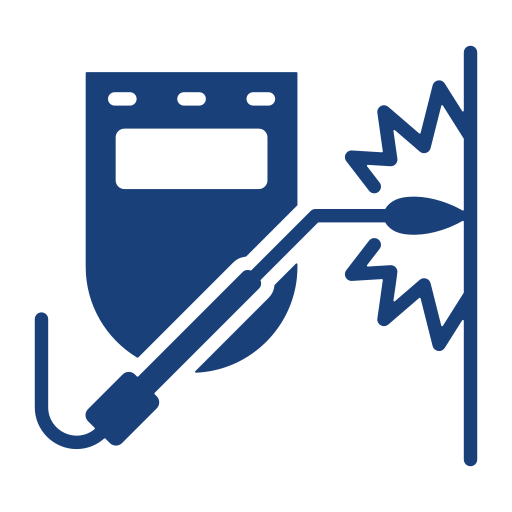
Steel and Metal Fabrication
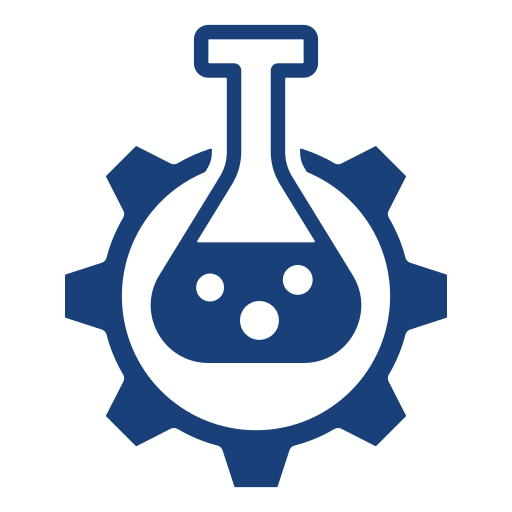
Chemical Processing
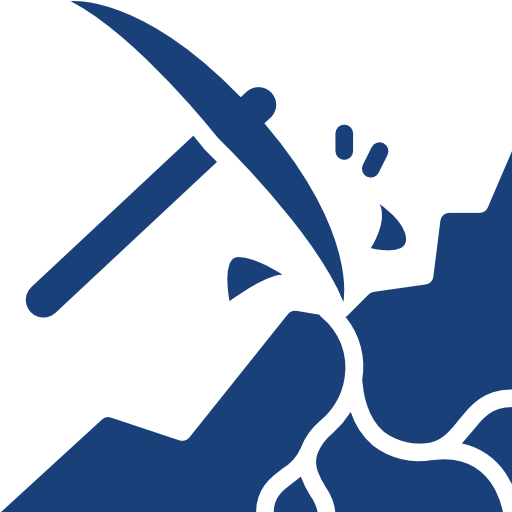
Mining and Mineral Processing
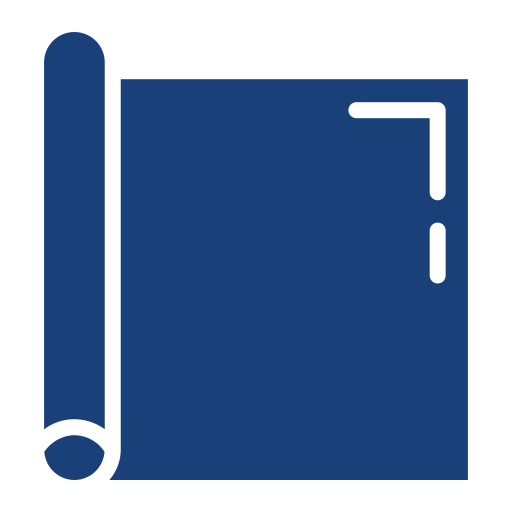
Pulp and Paper Production
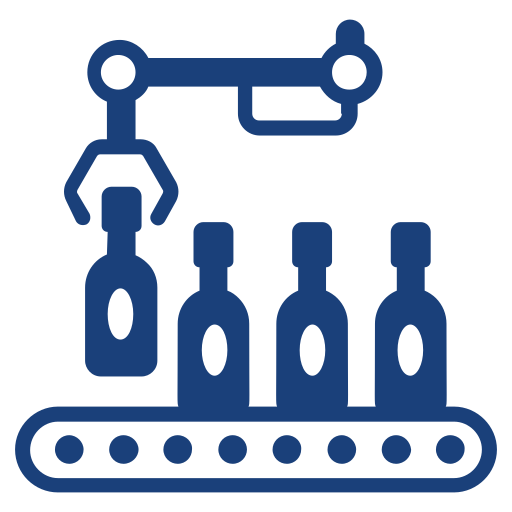
Food & Beverage Manufacturing
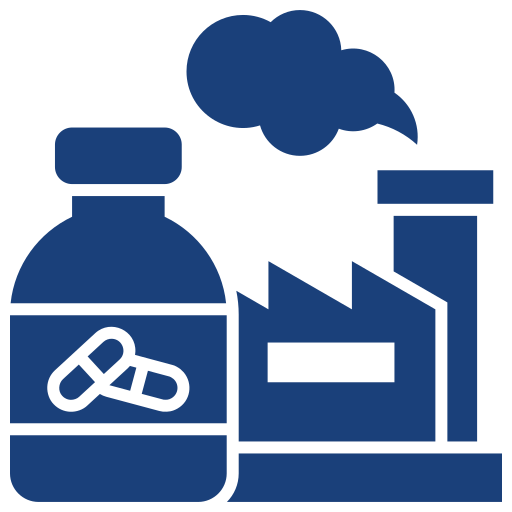
Pharmaceutical Production
Manufacturing Details
Reverse Engineering:
Inspected and disassembled existing damaged bags to analyze dimensions and material properties.
Retrieved original system drawings from the Great Lakes Filters database for reference.
Fabrication:
Produced filter bags using high-temperature resistant materials at the Hillsdale, MI facility.
Optimized bag design to ensure seamless integration and improved back pulse performance.
Quality Control Measures:
Material Testing: Evaluated for durability under high-temperature and corrosive conditions.
Fit Verification: Ensured precise alignment with the original tube sheet design.
Performance Validation: Conducted system smoke tests and pre-heating simulations to verify efficacy.
Quality Control Highlights
Great Lakes Filters implemented robust quality control protocols, including:
Value Delivered
This project showcases Great Lakes Filters’ ability to provide innovative, high-performance solutions for complex dust collection challenges. By combining reverse engineering, material optimization, and system redesign, the client achieved EPA compliance, reduced operational downtime, and improved facility productivity.