Engineering Precision in Flex Matt Assembly for Automotive Applications
Project Overview
Acme Mills, a trusted name in textile and materials solutions, successfully partnered with a leading global automotive seat and interior systems manufacturer to produce lightweight Dymetrol Flex Matt Assemblies. Applicable across the automotive seating market, these components are critical for ensuring durability, comfort, and structural integrity in vehicle seating systems.
This project focused on meeting stringent industry specifications, delivering on-time production, and adhering to rigorous quality control standards. These assemblies are intended for use in luxury SUVs, aligning with the client’s commitment to high-performance materials in automotive interiors.
Project Specifications
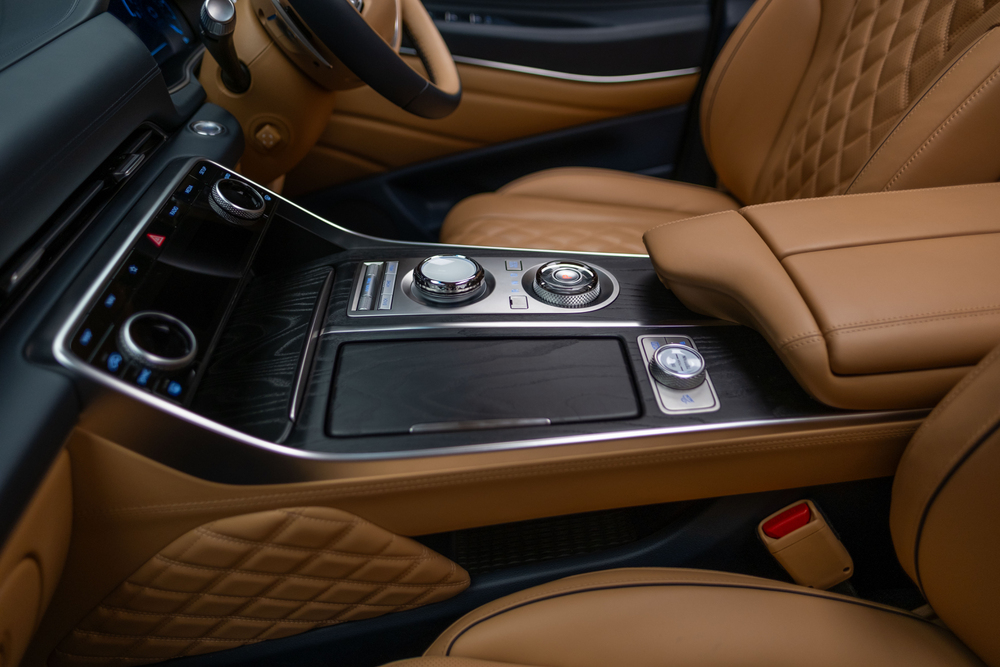
Quality Control Steps
To ensure the Dymetrol Flex Matt Assemblies met the highest quality and regulatory standards, Acme Mills leveraged its robust quality control framework, underpinned by relevant certifications and industry best practices.
- certifications
- Incoming Material Inspection
- In-Process Checks
- Final Inspection
- Annual Validation and Audits
Certifications Supporting Quality Control
Incoming Material Inspection:
- Lot certifications verified tensile strength, elongation, and flammability performance.
- Bond strength and dimensional consistency checks were conducted on each shipment.
In-Process Checks:
- Dimensional accuracy of cut pieces confirmed with calibrated yardage counters and templates.
- Regular inspections (first-piece, hourly, and last-piece) ensured seam consistency and compliance with tolerances.
- Operator verification ensured that all labels, including “D” marking for Dymetrol components, adhered to industry and client specifications.
Final Inspection:
- Comprehensive checks verified all parts against dimensional, material, and performance standards.
- Finished good labels and packaging were inspected for compliance with automotive labeling requirements and weight limits to ensure regulatory and client-specific conformity.
Annual Validation and Audits:
- Third-party laboratory testing confirmed ongoing compliance with FMVSS-302 and FAR 25.853 standards.
- Internal and supplier audits, managed through the Plex system, ensured alignment with CQI-23 and other relevant quality frameworks.
By integrating these certifications and quality practices, Acme Mills not only delivered precision-engineered assemblies but also instilled confidence in their ability to meet the exacting standards of the automotive industry.
Manufacturing Details
1. Material Preparation:
Material Standards: All incoming Dymetrol fabric rolls underwent certification checks to comply with FMVSS-302 flammability and FAR 25.853 standards.
Cutting: Advanced die-cutting machines (ATOM 2) were used for precise dimensions, ensuring tolerances of ±3 mm for cut lengths and widths.
2. Assembly Process:
Sewing Operations: Double-needle walking foot machines (4 mm and 6 mm gauges) were employed to ensure seam accuracy and strength.
Thread and Needle Selection: Ball-point needles marked with “SES” and FP4098 thread were specified to avoid fabric damage and ensure durability.
Positioning and Alignment: T-gauge fixtures verified the placement of retainers and fabric alignment perpendicular to structural components.
3. Packaging:
Primary Container: Custom corrugated boxes designed for optimal protection and storage efficiency.
Unit Load Efficiency: 76.32% trailer utilization was achieved using standardized wood pallets and stretch-wrapped unit loads.
Project Highlights
Acme Mills’ ability to capitalize on Dymetrol’s versatility and lightweight benefits highlights its expertise in delivering innovative solutions across a wide spectrum of automotive applications.
Acme Mills’ collaboration with the automotive manufacturer exemplifies its ability to meet complex manufacturing challenges with precision and reliability. The meticulous attention to material integrity, precision manufacturing, and quality assurance underscores Acme Mills’ position as a trusted partner in advanced automotive solutions.
Dymetrol’s lightweight and versatile properties make it an exceptional choice for automotive seating across all vehicle classes, offering unique advantages for efficiency and performance in both standard and luxury applications. The project not only achieved technical excellence but also supported broader industry goals of sustainability and innovation. This case study demonstrates how Acme Mills combines cutting-edge material solutions with stringent quality standards to drive success in demanding manufacturing environments.