Custom Slit Suspension Fabric for Marine Seating Applications
Project Overview
Acme Mills partnered with a leading luxury pontoon manufacturer to produce customized Dymetrol seat suspension fabric for use in high-end pontoon boat seating. The project required precision customization of the fabric’s width to meet strict design specifications while maintaining the durability, ergonomic performance, and aesthetic appeal critical to luxury marine applications. This collaboration exemplified Acme Mills’ commitment to delivering tailored solutions that align with client manufacturing needs and sustainability goals.
This project focused on ensuring on-time production, meeting precise material dimensions, and adhering to rigorous quality control processes. The Dymetrol fabric was utilized in captain’s chairs, passenger bench seating, and lounging areas, contributing to enhanced comfort and weight reduction across the seating systems.
Project Specifications
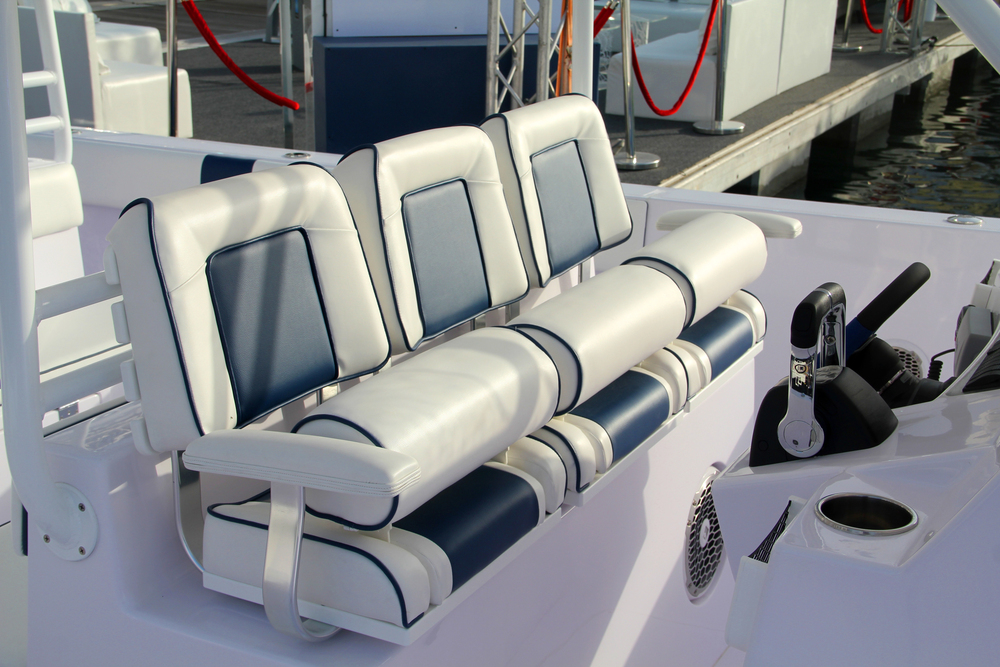
Quality Control Steps
Incoming Material Inspection:
- Material Certification: Incoming fabric rolls underwent certification checks to ensure consistency in tensile strength, elasticity, and color matching.
- Dimensional Verification: Rolls were inspected for accurate initial widths and length measurements before slitting.
In-Process Inspections
- Dimensional Accuracy: Calibrated equipment verified fabric widths during slitting and re-rolling processes to ensure tolerances were met.
- Structural Integrity Testing: Random samples were tested for load-bearing performance to simulate real-world usage.
Final Inspection:
- Visual and Mechanical Assessment: Each roll was inspected for uniformity, defects, and adherence to client specifications.
- Packaging Review: Final inspection of packaging ensured that rolls were appropriately labeled, secured, and prepared for shipment.
Manufacturing Details
1. Material Preparation:
Base Material: The base fabric used was a woven polyester/Hytrel composite (C200 Dymetrol, white, 86-inch width, 82-inch usable).
Yarn Specifications: NE 24/2 airjet-spun 100% polyester yarn.
2. Customization and Processing
Slitting and Re-Rolling: The wide fabric rolls were slit to 15-inch widths using precision slitting equipment, ensuring consistency across the entire batch.
Stiffening Treatment: The fabric was processed to meet required load-bearing properties through a stiffening procedure to enhance durability and performance.
3. Subcontracted Weaving
The weaving process reinforced the strength and resilience of the fabric to meet marine seating specifications, with subcontractors adhering to Acme Mills’ stringent manufacturing guidelines.
Project Highlights
This project demonstrates Acme Mills’ expertise in delivering innovative, custom-engineered fabric solutions that meet the stringent requirements of luxury marine seating. By integrating advanced manufacturing techniques, rigorous quality controls, and sustainability-focused practices, Acme Mills provided a seating solution that met the client’s needs for comfort, performance, and environmental responsibility. The partnership underscored Acme Mills’ commitment to excellence in material science and manufacturing for specialized applications.