Precision Textile Cutting
Program and die-cut Custom Fabric, Filter, and Pad Solutions for Diverse Industries
PROGRAM CUTTING
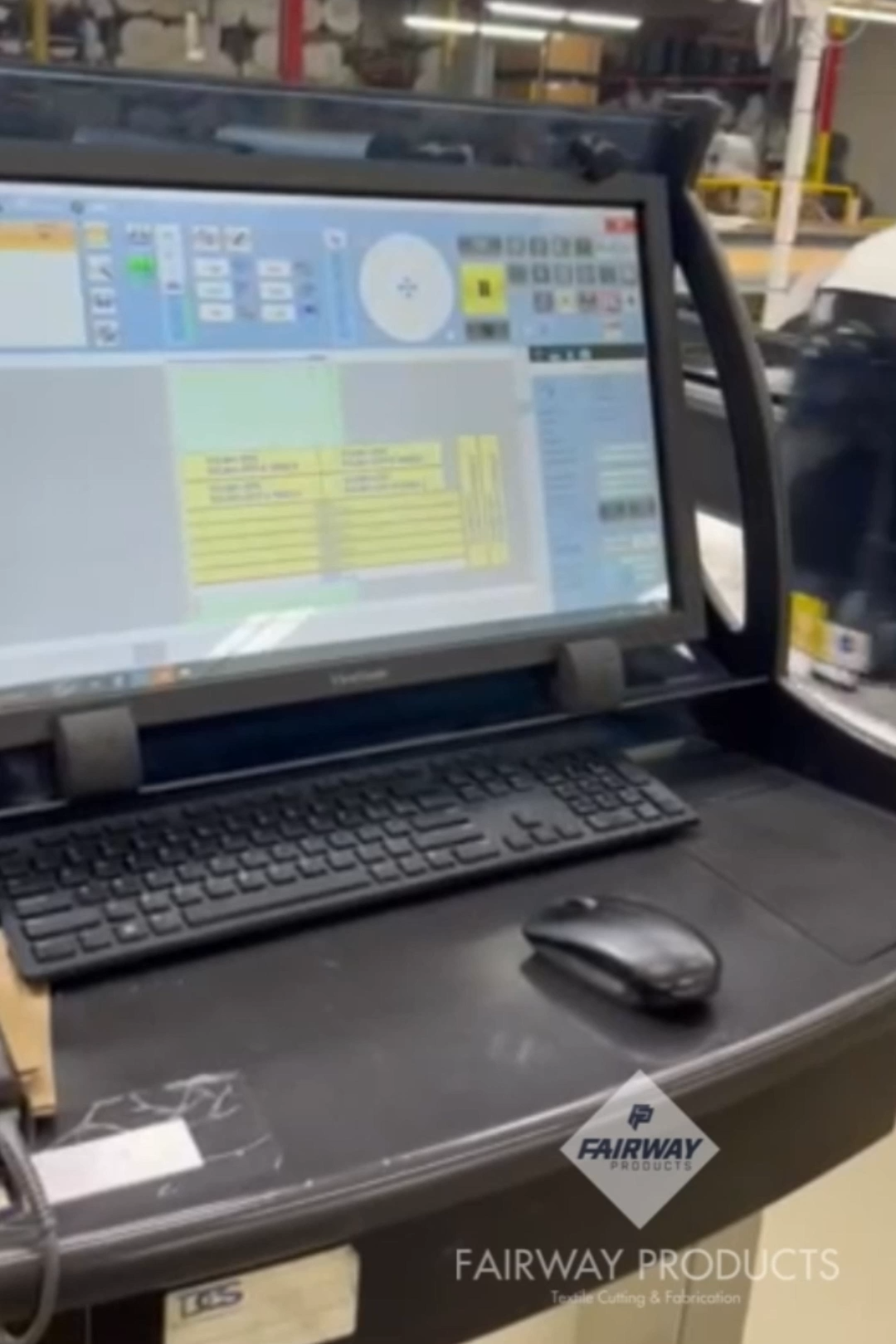
For over six decades, Fairway Products has been a leading provider of precision die-cut and program-cut components, specializing in fabrics, filters, and pads for a wide range of industries, including medical, automotive, and pharmaceutical. Our commitment to quality, innovation, and customer satisfaction has made us a trusted partner to businesses worldwide.
Leveraging state-of-the-art CAD systems, our expert team optimizes material usage to deliver cost-effective and high-quality die-cut and program-cut components. From intricate shapes to complex patterns, we offer tailored solutions to meet your exact specifications. Whether you require small-batch prototypes or large-scale production runs, we have the capacity and expertise to handle your project efficiently.
DIE CUTTING
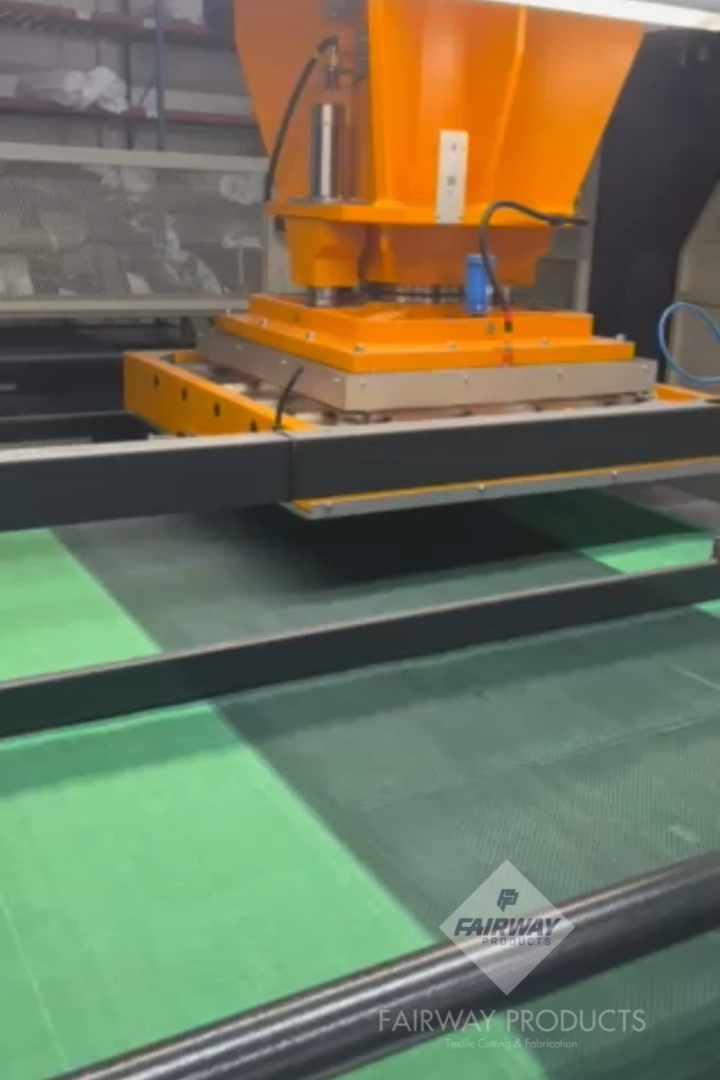
Our Filpaco filter papers renowned for their exceptional performance and versatility are available in a variety of grades, which can all be custom cut to suit the unique requirements of your filtration process. From fine particulate removal to liquid clarification, we have the ideal filter paper solution that can be cut to fit your exact application.
Our comprehensive services extend beyond die cutting and program cutting and filter paper production. We offer expert consultation to help you select the optimal materials and configurations for your specific needs. Our prototyping capabilities allow you to visualize and refine your product before committing to full-scale production. Additionally, our experienced technicians provide ongoing support to ensure your complete satisfaction.
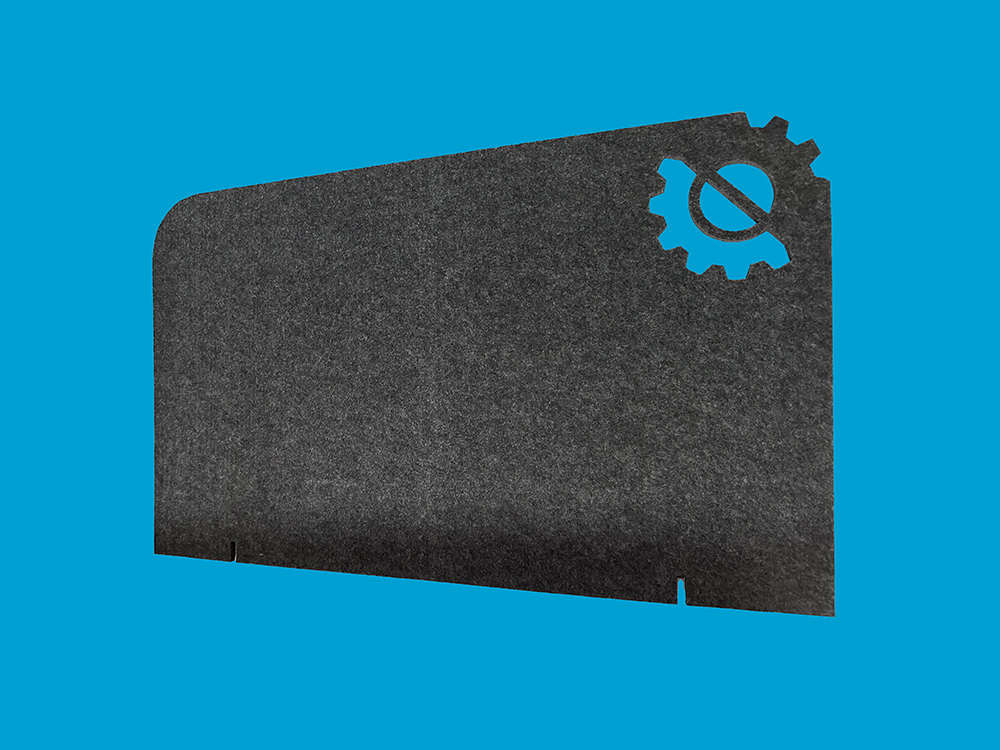
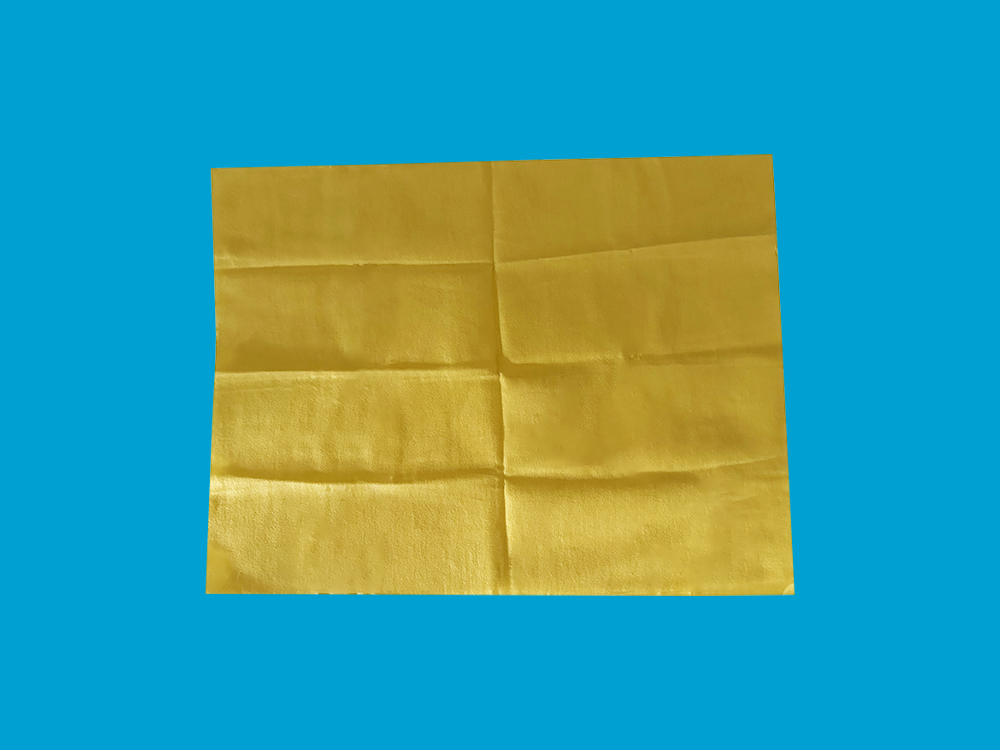
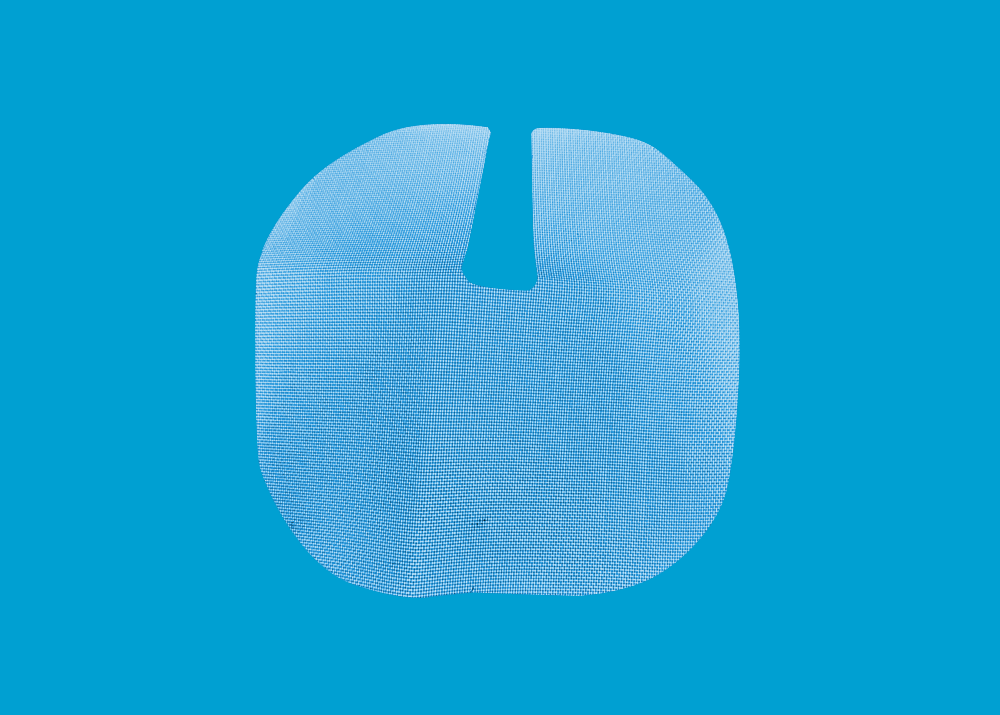
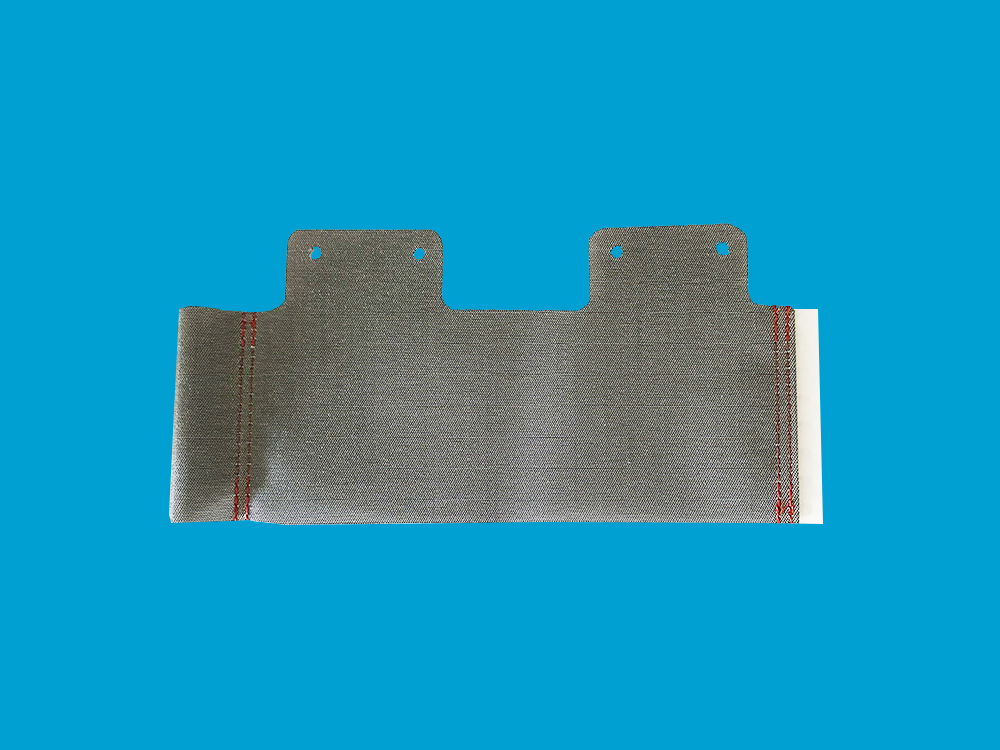
The Power of Fairway
Do you need custom fabric, filter, or pad solutions? Fairway Products offers a comprehensive die cutting and program cutting service for various industries. We utilize advanced technology and expertise to deliver precise cuts, reduced waste, and efficient production. From medical dressings to automotive gaskets, our capabilities cater to a wide range of applications. Explore the benefits of Fairway’s precision cutting and discover how we can streamline your manufacturing process.
Applications
Medical & Hygiene
Dressings, filters, swabs, wipes, bandages
Seating & Seat Covers
Buses, Airplanes, RVs, ATVs, Trucks
Filtration
Dust collection, oil mist, fabric/textile pre-filters, HVAC filters
Industrial Manufacturing
Gaskets, wipes, insulation
Features
Precision Cutting:
- Gerber and Pathfinder cutters for accurate results
- Handles materials up to 90″ wide and 1.5″ thick
- Drilled holes from 1mm to 6mm
- Tension-free spreading for textiles
Custom Solutions:
- No tooling required for program cutting
- Easy program modifications
- Steel rule dies for intricate designs
- Multi-ply cutting capabilities
Material Versatility:
- Processes a wide range of textiles, non-wovens, films, and papers
- Cuts materials up to 2″ thick (slitting)
- Handles roll widths up to 104″ (slitting & rerolling)
Advanced Capabilities:
- Nesting for material optimization
- Slitting and rerolling with tight tolerances (+/- 1.5mm)
- Duplex slitting for thin films and paper
Benefits
Key Capabilities
Materials & Equipment
Materials
Key Markets
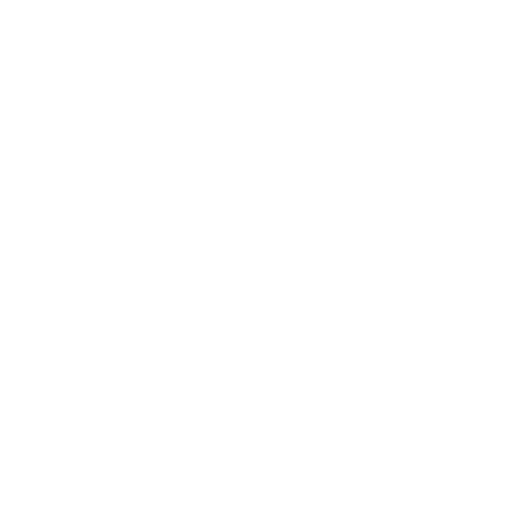
Automotive
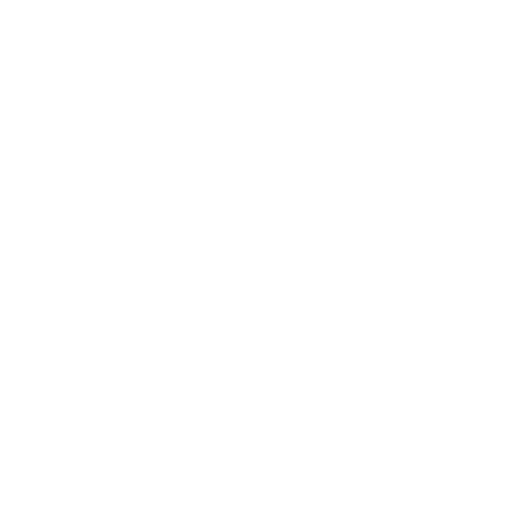
Industrial
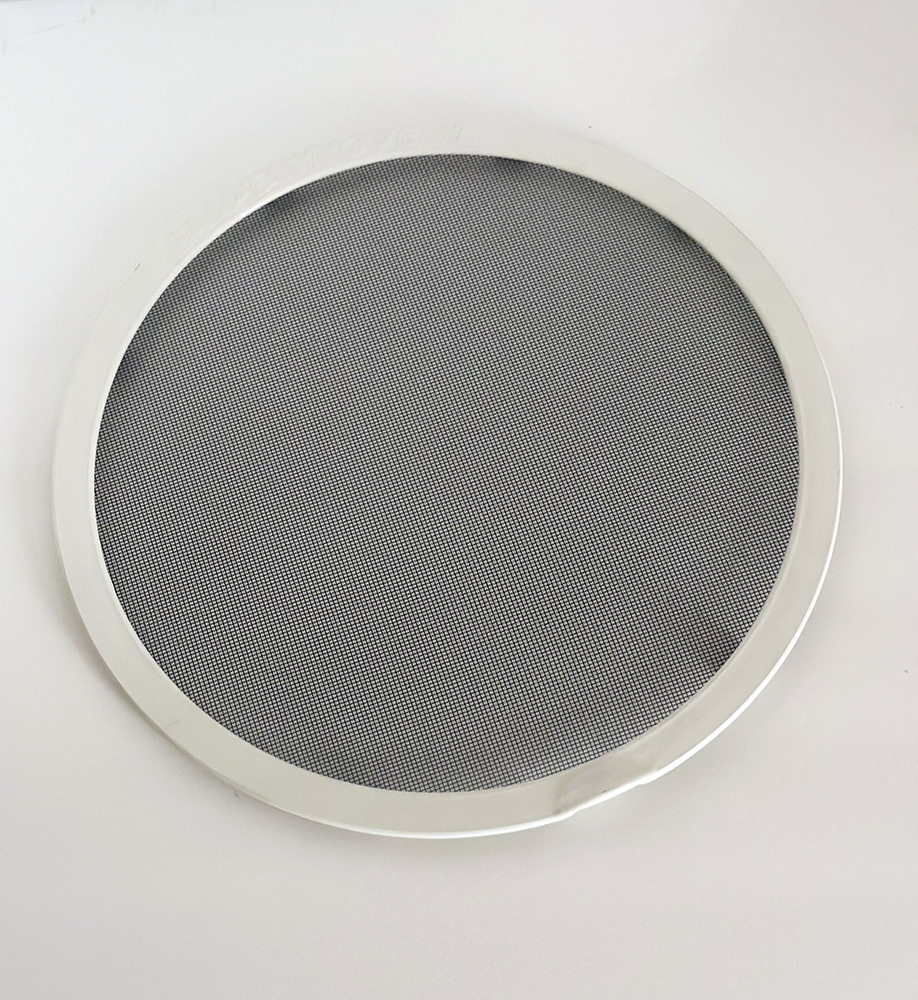
Project Specifications
Uses and Applications
The RV screens manufactured in this project are designed for installation in recreational vehicles, providing durable and reliable screening solutions. These screens are essential components for RV windows, ensuring ventilation while keeping insects and debris out.
Scalability of the Project
The initial run of this project demonstrated Fairway Products’ ability to scale production efficiently. Starting with a pilot batch, the process was refined and optimized to handle larger volumes, ensuring consistent quality and timely delivery. The scalability of the project underscores Fairway’s capability to meet increasing demands without compromising on precision or performance.
Manufacturing Process
Die-Cutting
Rolls of aluminum screen are processed through a die-cut machine to achieve the required shapes.
Refrigeration of Frames
Molded plastic frames are chilled using a refrigerated unit to ensure precise expansion during the heat-staking process.
Heat-Staking
The die-cut screens are heat-staked to the chilled plastic frames. As the frames return to room temperature, they expand slightly, ensuring the screens remain taut and wrinkle-free.
Quality Control
Each RV screen undergoes rigorous quality checks to ensure adherence to specifications and ISO 9001:2015 standards.
Quality Control Steps
Fairway Products adheres to strict quality control measures throughout the manufacturing process:
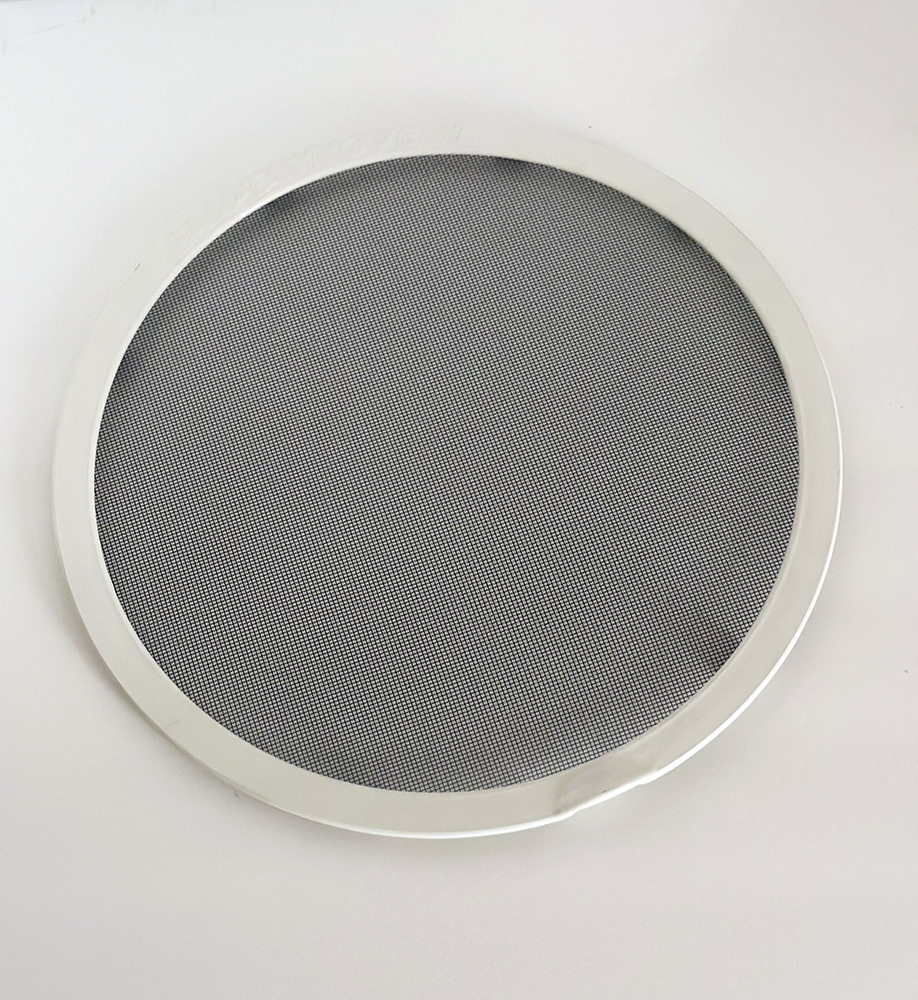
Value to the Customer: By handling both the die-cutting and the heat-staking processes, Fairway Products provided a turnkey solution that streamlined the customer’s supply chain. This integration allowed the customer to receive ready-to-install RV screens, reducing assembly time and costs. The innovative use of refrigeration to maintain screen tension added a unique value, ensuring a superior product that enhances the end-user experience.
Fairway Products’ ability to deliver high-quality, scalable solutions with strict adherence to quality standards exemplifies their commitment to excellence in manufacturing. This project not only met but exceeded the customer’s expectations, solidifying Fairway Products as a trusted partner in the RV industry.