Precision Cutting, Endless Possibilities
Transform Your Materials with Our Expert Slitting and Rerolling Services
Fairway Products has a long history in slitting and rerolling, dating back to 1951. Our parent company, Acme Mills, also has a rich century long history in developing technical fabrics and textile converting programs.
Fairway slits and rewinds your rolled goods with a quick turnaround time, and stocking capabilities. In addition to converting your existing rolled goods, we can often source material at a more competitive price point leveraging the Acme Group’s purchasing team.
Our capabilities and equipment can process a wide variety materials, wovens, knits, paper, films, adhesives, non-wovens – bring it in. We are ready to help you optimize and re-invent your product.
We partner with a large group of vendors and suppliers resulting in a very expansive list of offerings and services.

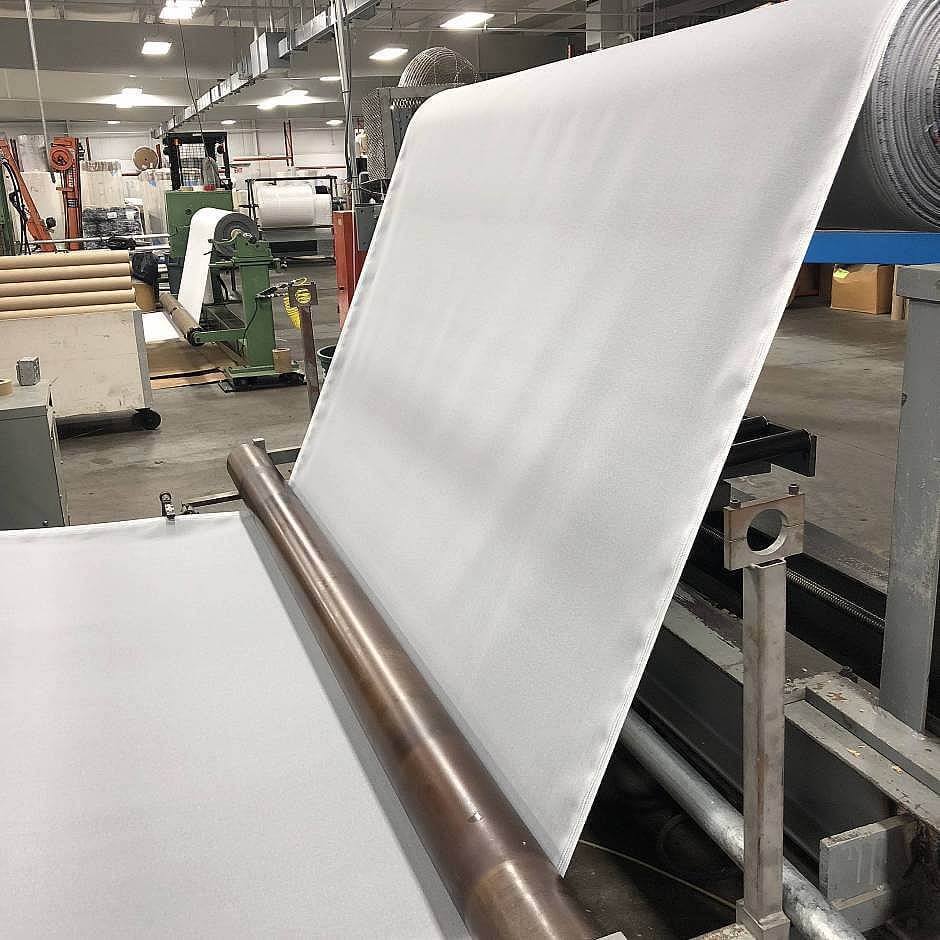
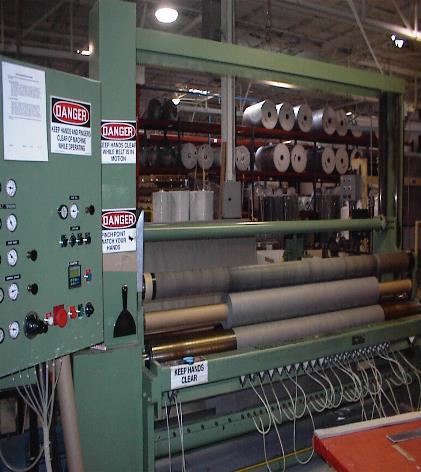
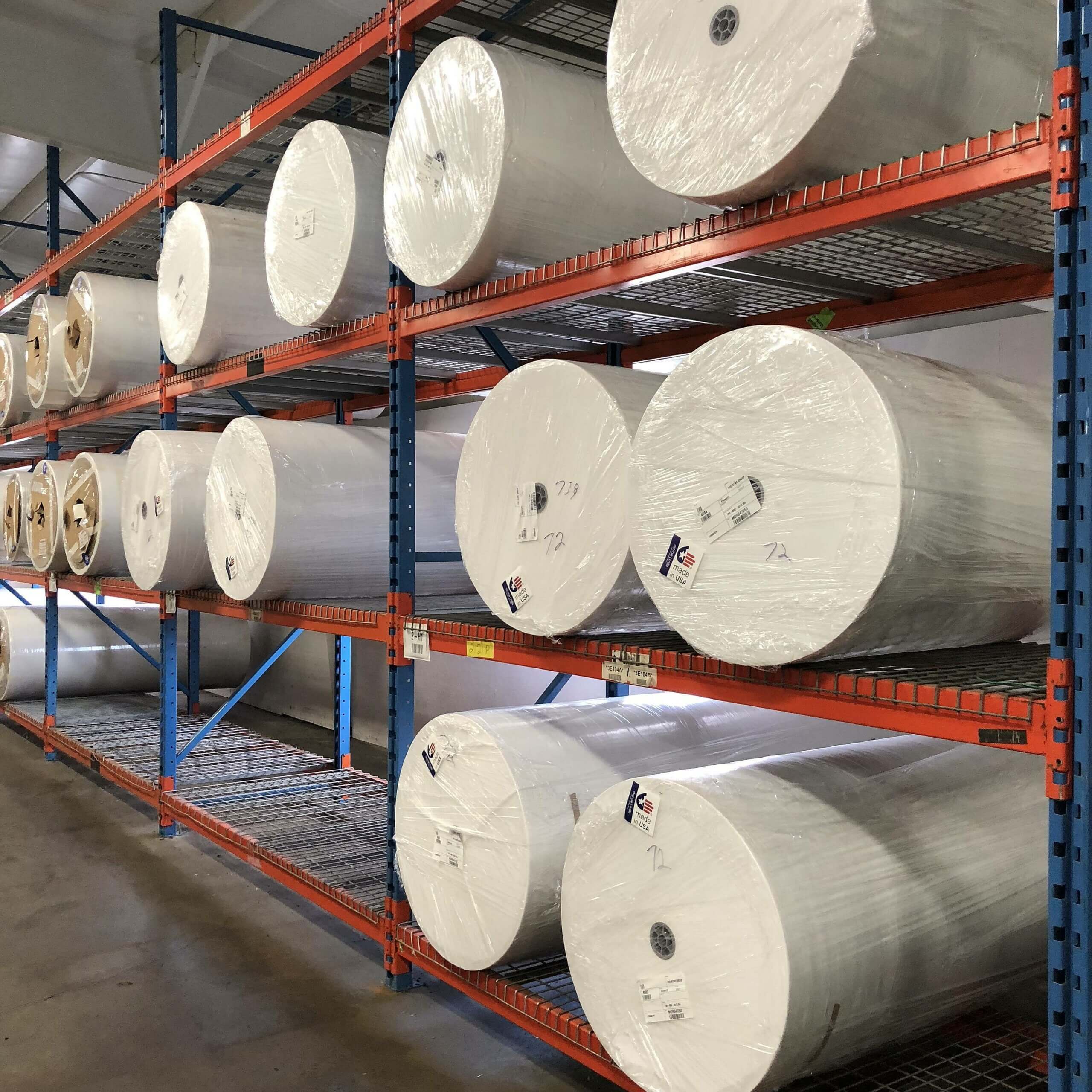
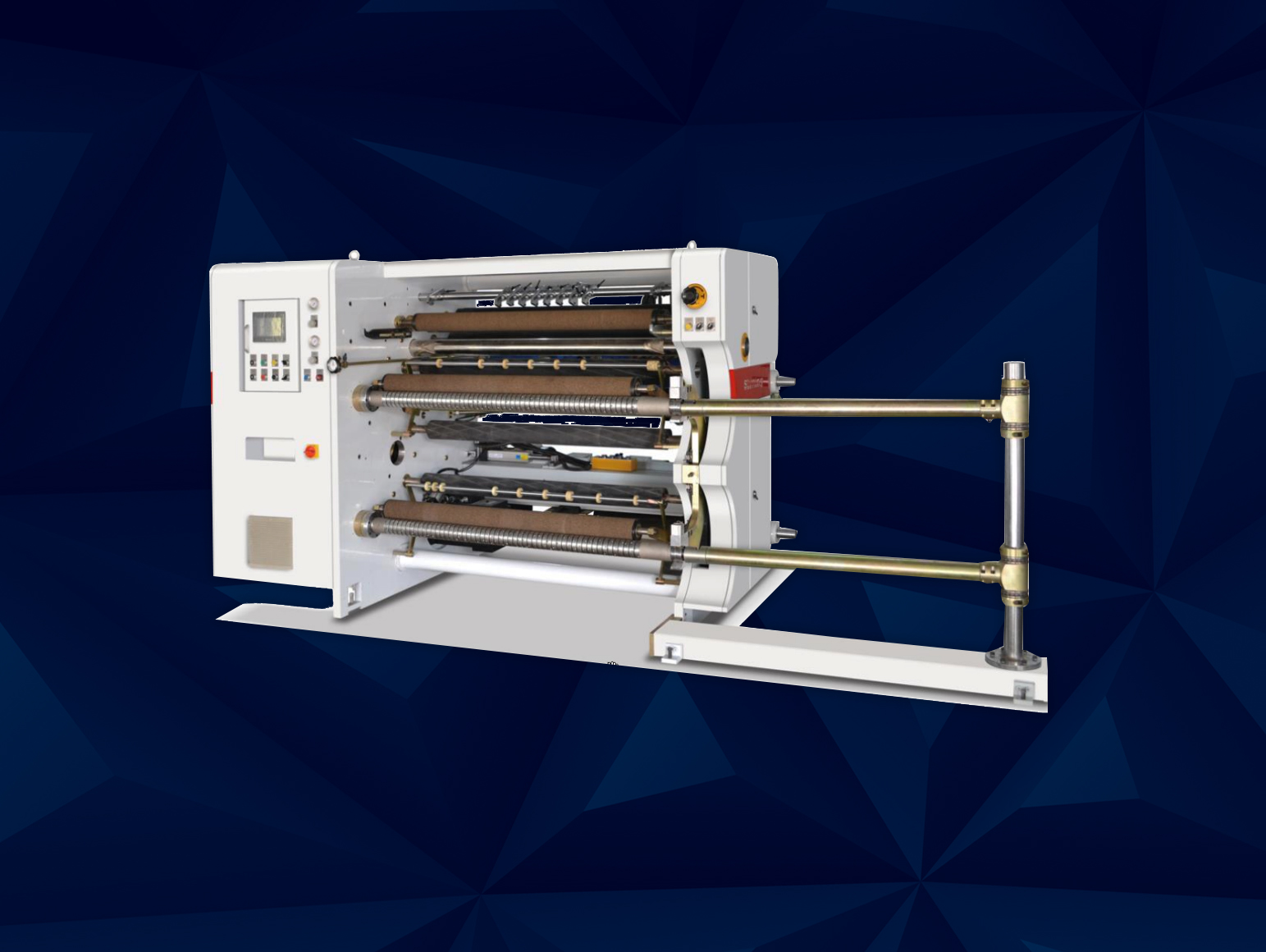
The Power of Fairway
Fairway Products unlocks the full potential of your materials through precision slitting and rerolling. Our state-of-the-art equipment and extensive expertise enable us to transform your raw materials into high-quality, customized products. From automotive components to industrial filtration, Fairway Products delivers unmatched precision, efficiency, and cost-effectiveness. Experience the Fairway difference and discover how our solutions can elevate your manufacturing process.
Applications
Seat covers, headliners, carpets, insulation, sealing tapes
Crop covers, mulch films, geotextiles
Surgical drapes, gowns, masks, wound care products
Air filters, liquid filters, industrial filtration media
Features
Benefits
Slitting and Rerolling Capabilities
Non-Wovens
Wovens
Paper & Advanced Material
Materials & Equipment
Specifications
Materials
Key Equipment
Key Markets
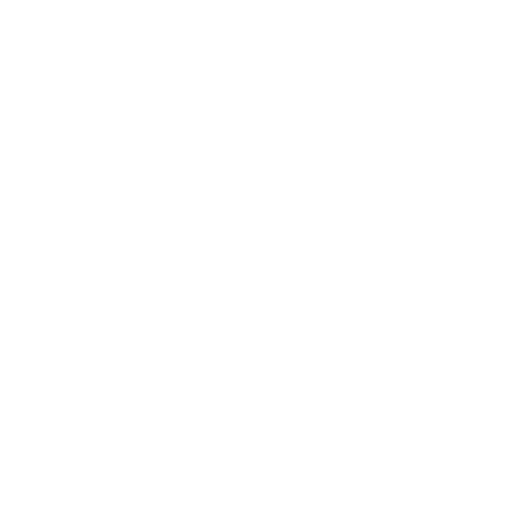
Automotive
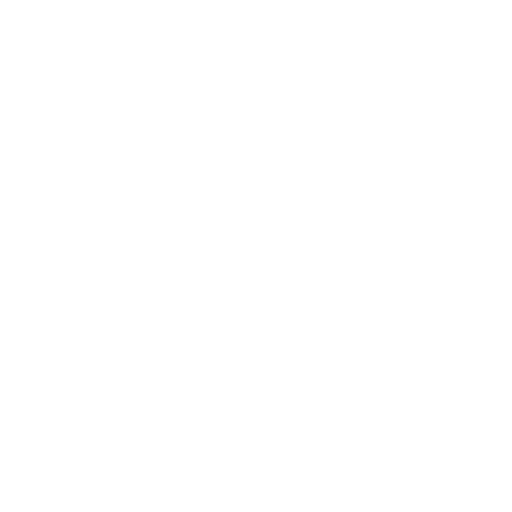
Aerospace
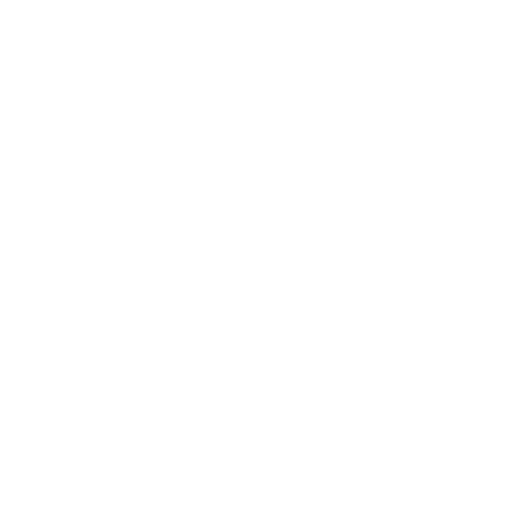
Textiles
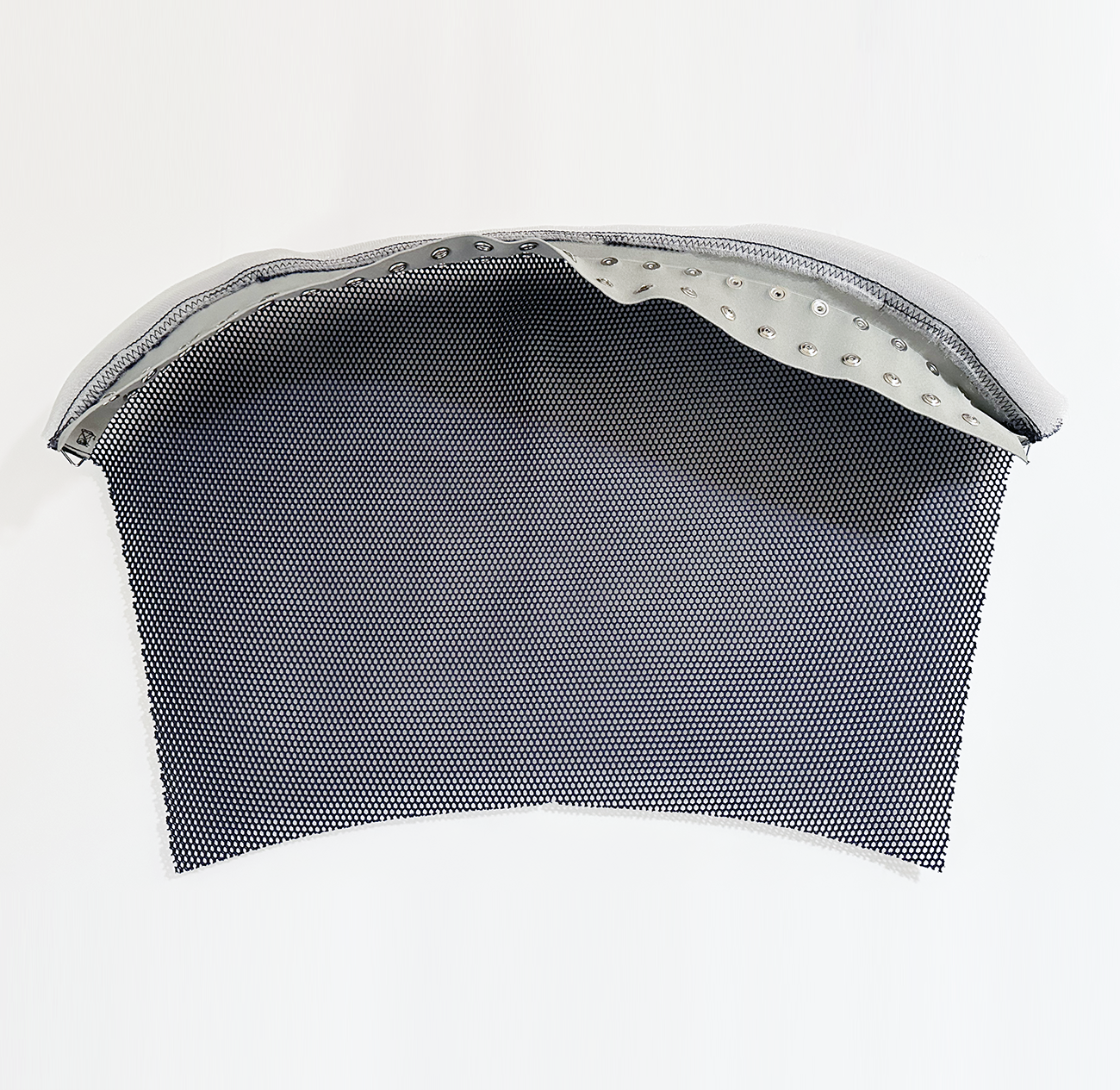
Project Specifications
Uses and Applications
The heavy-duty truck bug screens manufactured by Fairway Products are essential for protecting the front grills of commercial-grade trucks. These screens are critical for preventing insects, debris, and other potential hazards from damaging the vehicle’s radiator and other front-end components during long-haul trips.
Scalability of the Project
The initial run of the heavy-duty truck bug screens project demonstrated Fairway Products’ ability to scale production efficiently. The collaboration began with an initial batch of 5,000 units to fine-tune specifications and ensure quality. Following the successful initial run, the project scaled up to meet the client’s growing demands. Fairway Products’ advanced manufacturing capabilities allowed for seamless scalability, ensuring timely delivery and consistent quality.
Manufacturing Process
Material Selection & Preparation
The project began with the selection of high-quality vinyl and aluminum screen materials, chosen for their durability and effectiveness in protecting against debris.
CNC Cutting
Using advanced CNC cutting techniques, Fairway Products precisely cut the vinyl and aluminum screen materials to the exact dimensions specified by the client. This process ensured accuracy and consistency across all units.
Industrial Sewing
Skilled staff operated industrial sewing machines to assemble the cut materials into finished bug screens. This step was critical in maintaining the structural integrity and durability of the screens.
Final Assembly
After sewing, the bug screens underwent a final assembly process where additional components, such as mounting brackets, were added as per the client’s specifications.
Quality Control Steps
To ensure the highest quality of the heavy-duty truck bug screens, Fairway Products adhered to rigorous quality control measures throughout the manufacturing process:
Client Benefits
By collaborating with Fairway Products, the client gained significant productivity advantages. Fairway Products’ efficient production processes provided essential capabilities that were not available in-house, allowing the client to focus on other critical products within their facility. The expanded production capabilities enabled the client to meet growing demands without compromising on quality.
Certifications
Fairway Products is proud to maintain ISO 9001:2015 certification, reflecting their commitment to quality management and continuous improvement.
Conclusion
Fairway Products’ expertise in CNC cutting and industrial sewing, combined with their dedication to quality, made them the ideal partner for this heavy-duty truck bug screen project. The successful collaboration not only enhanced the client’s productivity but also demonstrated Fairway Products’ capability to deliver high-quality commercial truck components on a large scale.