Custom Die-Cut Filters for Commercial Fryers in the Food & Beverage Industry
Needs Assessment & Solutions Summary
Filpaco collaborated with a leading OEM in the Food & Beverage industry to design and manufacture custom-sized fryer filters for their commercial fryers. The project leveraged precision die-cutting and private label manufacturing to meet the client’s unique requirements.
By utilizing Filpaco Textiles, known for their exceptional filtration properties and industry versatility, the project successfully addressed the client’s needs. These solutions enabled the client to establish a profitable aftermarket replacement filter program by matching production with specific demands, reducing inventory and packaging costs, and streamlining operations.
Project Specifications
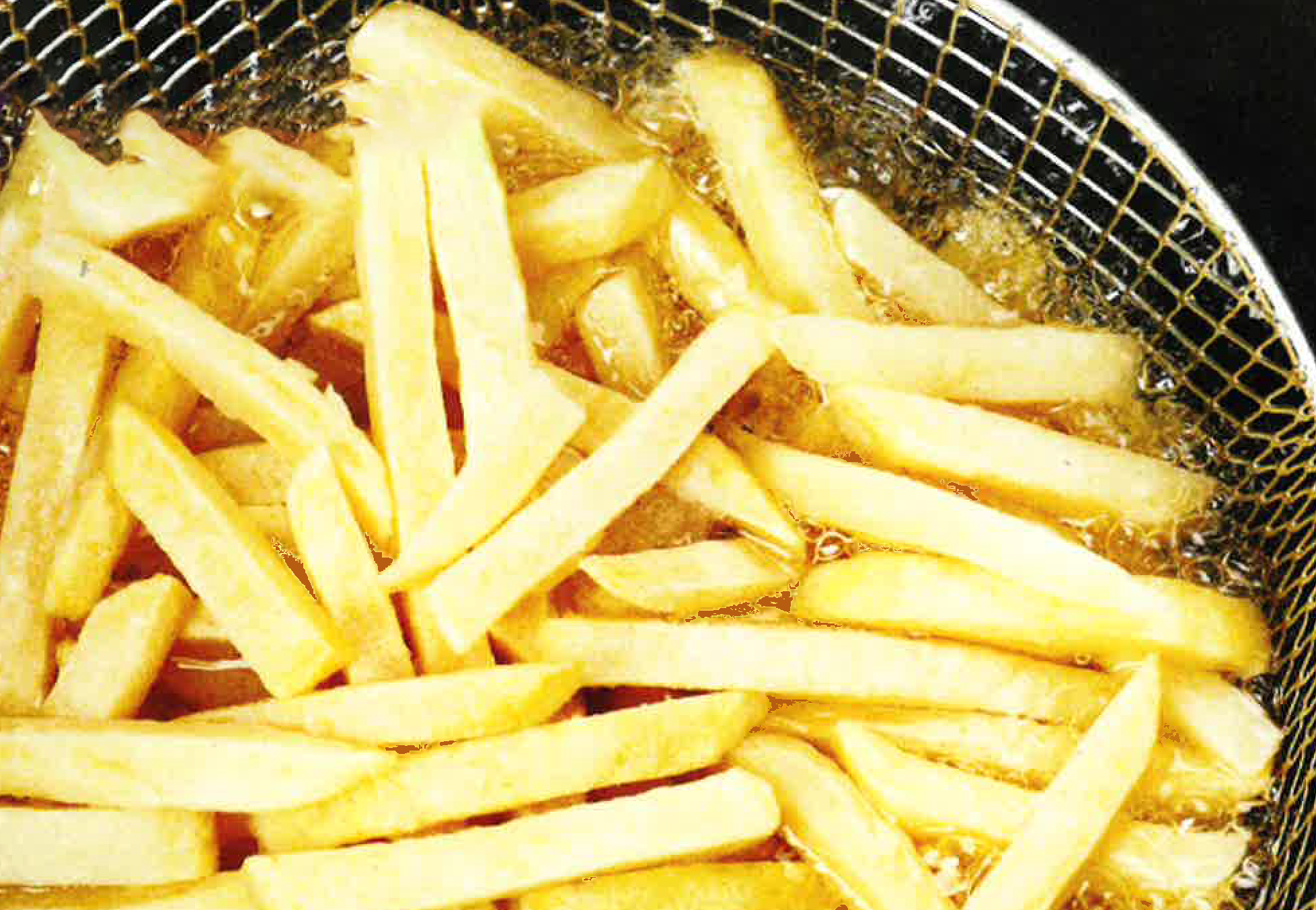
- Primary Applications: Filpaco Textiles enabled superior oil filtration, enhancing fryer performance, extending oil life, and maintaining food quality. These filters are specifically designed for use in high-volume commercial fryers, where maintaining equipment functionality and food safety is critical.
- Capacity: The solution scaled with the client’s aftermarket sales, providing a steady supply of replacement filters without excess inventory.
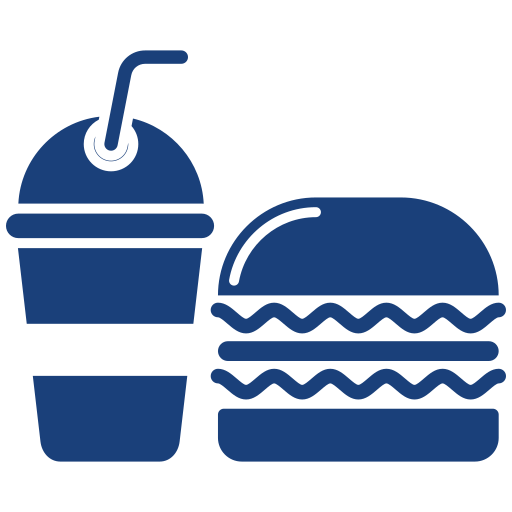
Fast Food Chains
High-capacity fryer filtration to maintain oil quality and reduce operating costs.
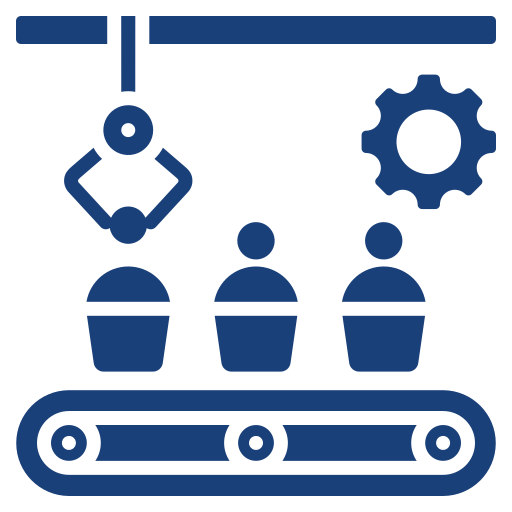
Food Processing Plants
Ensuring compliance with health regulations and enhancing production efficiency.
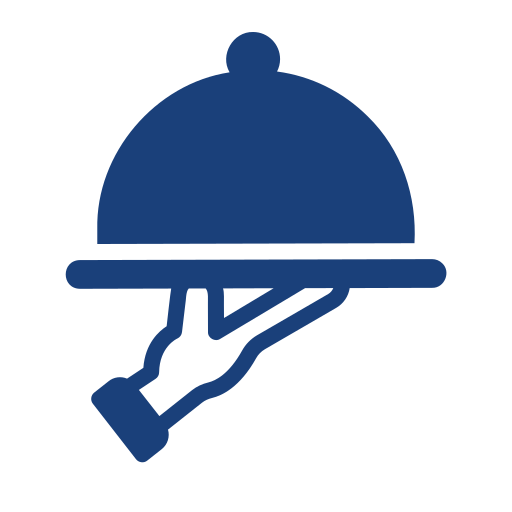
Hospitality Industry
Restaurants and caterers benefit from efficient filtration systems for extended oil usage.
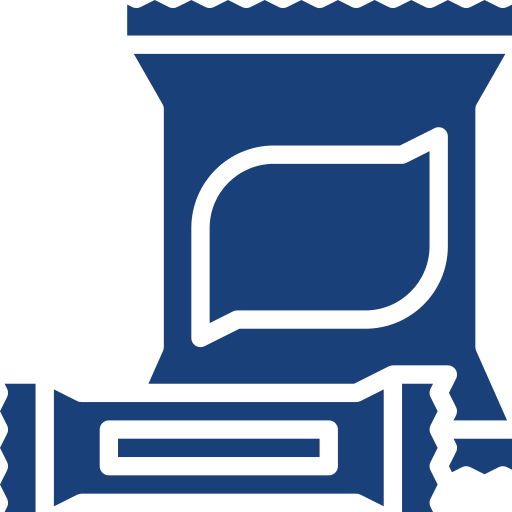
Snack Food Manufacturing
Filtration for fryers used in producing
chips and other snack foods.
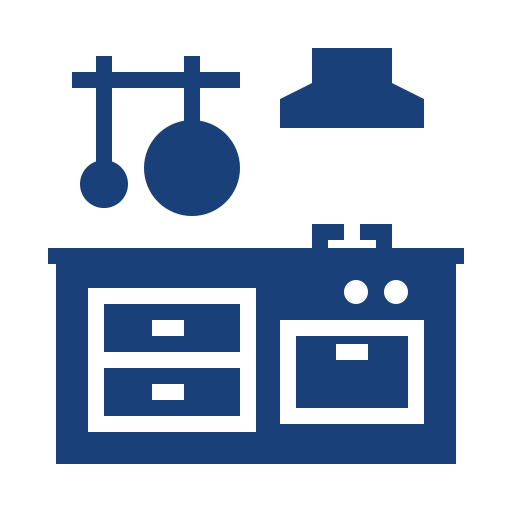
Industrial Kitchens
Large-scale meal preparation facilities, including schools,
hospitals, and corporate dining halls.
Manufacturing Details
Material Selection:
Filters were manufactured using high-quality Filpaco Textiles. These filter papers are recognized for their ability to handle fine particulate removal and liquid clarification, making them ideal for oil filtration in commercial fryers. Their compliance with FDA and NSF standards ensures they meet stringent safety and quality requirements for food industry applications as well.
Die-Cutting Process:
Custom tooling ensured accurate and efficient production of uniquely sized filters.
Filpaco Textiles’ versatility and multiple grades allowed us to optimize the filter properties for efficient oil filtration and extended fryer performance.
Private Label Packaging:
Packaging solutions were tailored to the client’s branding and optimized to reduce material and shipping costs.
Quality Control Measures
Value Delivered
This project demonstrates Great Lakes Filters’ ability to deliver tailored filtration and packaging solutions for the Food & Beverage industry. By combining precision die-cutting with the advanced properties of Filpaco Textiles and turn-key private label manufacturing, we empowered the client to achieve cost efficiencies, operational improvements, and a profitable aftermarket program.