In fluid filtration and separation, precision is paramount. Great Lakes Filters’ Die Cut Filter Discs deliver exceptional performance, ensuring clean processes across industries. This blog delves into the science behind these innovative discs and their technical applications, offering engineers and technical professionals insights into their design, materials, and performance capabilities.
The Science Behind Die Cut Filter Discs
At their core, die cut filter discs function as barriers, capturing particles while allowing fluids or gases to pass through. Their effectiveness hinges on the material’s pore size, porosity, and chemical compatibility. The die-cutting process ensures precision manufacturing, where discs are shaped to exacting tolerances, minimizing edge fraying and ensuring uniformity.
The material science behind these discs includes woven and nonwoven fabrics, polymer-based membranes, and metallic meshes. These materials are chosen for their ability to withstand specific chemical, temperature, and mechanical stresses while maintaining filtration accuracy.
Technical Details and Applications
Great Lakes Filters offers discs in a variety of materials, each tailored for specific applications:
Die-cut filter discs are manufactured to exact dimensions, ensuring a perfect fit within filtration systems. This precision minimizes bypass and leakage, maintaining optimal system performance.
Available in a range of micron ratings, these discs cater to both coarse and fine filtration needs. Their consistent pore structures ensure reliable particle retention, critical for processes in medical device manufacturing and industrial chemical production.
Applications Across Industries
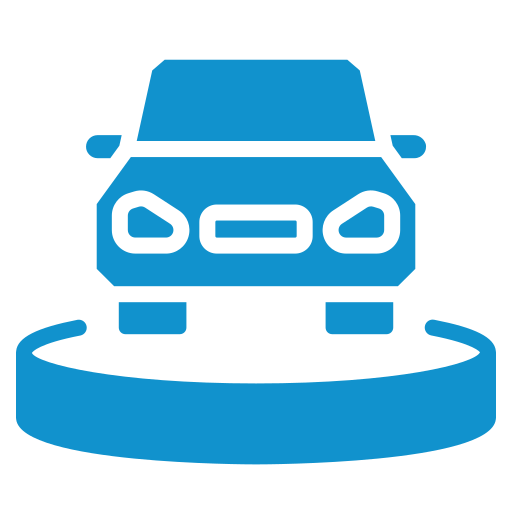
Automotive
Die-cut discs are integral to oil and fuel filtration systems, where their precision ensures engine efficiency and longevity.
Pharmaceuticals
These discs provide sterile filtration for liquids and gases, adhering to strict regulatory standards.
Industrial Processes
From coolant filtration in machining to chemical separation, their durability and efficiency enhance operational reliability.
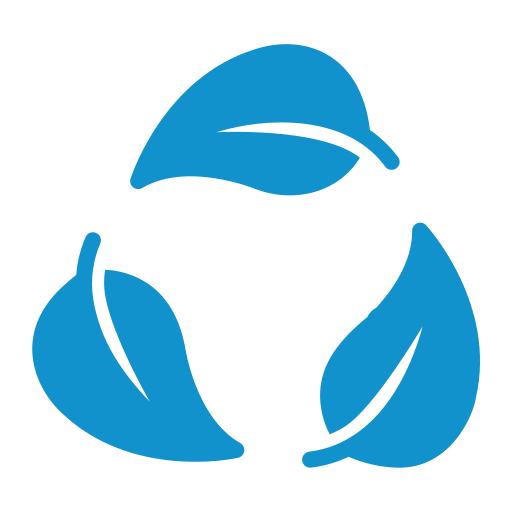
Environmental Systems
Used in water and air filtration, die-cut discs help maintain compliance with environmental standards.
Conclusion
Die Cut Filter Discs from Great Lakes Filters represent the pinnacle of precision and reliability in filtration technology. By combining advanced materials, customizable designs, and technical expertise, they meet the rigorous demands of engineers across industries. Whether your application involves high temperatures, corrosive chemicals, or stringent cleanliness standards, these discs deliver optimal performance.