The Science and Technology of Needle Punch Fabrics: A Deep Dive for Engineers
Understanding Needle Punch Fabrics
Needle punch fabrics are a critical innovation in nonwoven textiles, offering durability, adaptability, and precision-engineered performance. These fabrics are created by mechanically bonding fibers through a process that involves repeated penetration with barbed needles. This entanglement of fibers results in a material that is strong, uniform, and suited to a variety of technical applications.
The science behind needle punch technology combines material selection with precise control over fiber entanglement, ensuring that the fabric meets specific requirements for strength, flexibility, and dimensional stability. The ability to customize material properties through fiber type, needle density, and processing conditions makes needle punch fabrics highly versatile in industries such as automotive, filtration, and industrial applications.
Technical Applications of Needle Punch Fabrics
One of the primary uses of needle punch fabrics is in the automotive industry, where they must meet rigorous engineering standards for strength, weight, and durability. These fabrics are designed to provide structural support and functional benefits in interior and exterior vehicle components. Their composition and manufacturing process allow them to meet performance specifications related to mechanical strength, environmental resistance, and safety compliance.
Material Properties and Performance
Needle punch fabrics are engineered to provide precise performance characteristics, including:
Durability Under Dynamic Conditions
Needle punch fabrics are designed to perform reliably under fluctuating environmental conditions. Some of the key durability features include:
Performance Testing and Quality Assurance
These fabrics undergo rigorous laboratory testing to validate their performance:
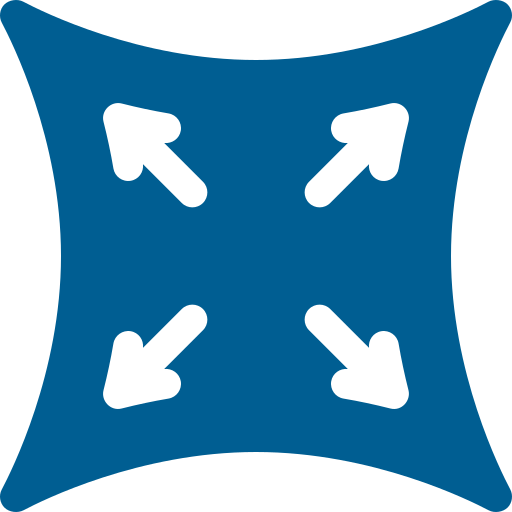
Strength and elongation tests confirm their ability to withstand mechanical stress without excessive deformation.
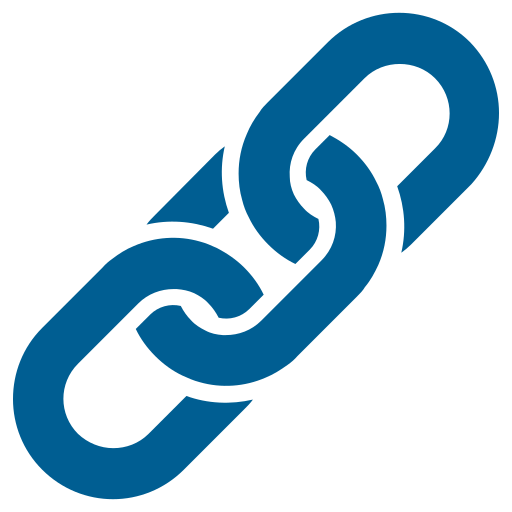
Tear resistance evaluations ensure long-term durability under high-stress conditions.
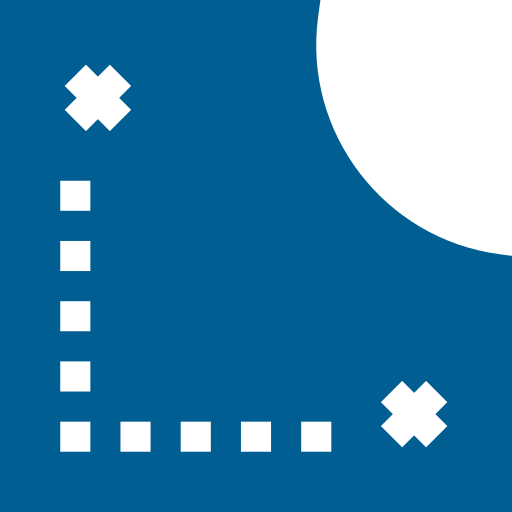
Seam strength and stretch properties are tested to verify flexibility and reliability in different applications.
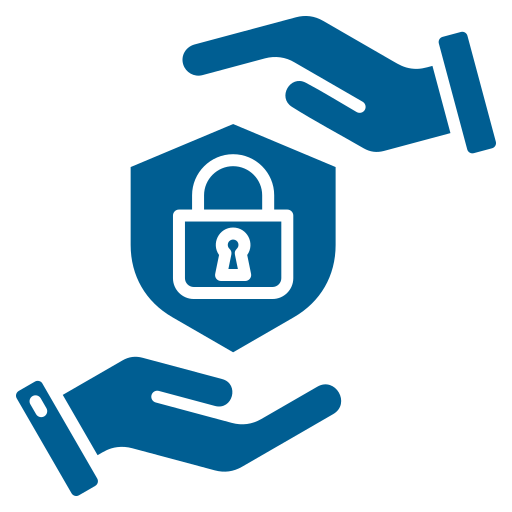
Compliance with flammability and safety standards to meet industry regulations and ensure secure use in automotive and industrial environments.
Applications in Engineering and Manufacturing
Needle punch fabrics are widely used in various engineering applications due to their combination of strength, adaptability, and compliance with industry standards. These applications include:
Conclusion
Needle punch technology represents the intersection of material science and engineering precision. These fabrics provide a high-performing, adaptable solution for industries that require durability, strength, and environmental resistance. Their compliance with strict quality standards ensures they remain a reliable choice for engineers seeking advanced material solutions for demanding applications.